Driverless transport systems – a game changer in intralogistics
More automated, more sustainable, more flexible – how experts see the future of intralogistics. Driverless transport systems are an integral part of intelligently controlled transport.
These systems are continuously evolving and are excelling in numerous applications worldwide. To ensure efficient material flow, however, the peripherals are just as crucial as the vehicle itself. The first crucial question is: DTV, AGV, DTS or AMR? There are a lot of different terms going around, all of which describe the use of specific robot technologies to automate processes. At item, we refer to this topic as mobile robotics. Another generic, overarching term is “driverless transport system” (DTS), which describes a system that uses “driverless transport vehicles” (DTVs) to transport materials and goods from A to B. There are different types of DTVs, however. First, there are automated guided vehicles (AGVs). These are track-guided, meaning they follow a predefined route that does not change. AGVs automatically stop when they encounter obstacles. The vehicles boast exceptional reliability and efficiency when it comes to handling transport tasks. However, if processes change, reconfiguring the fixed route network requires a great deal of work.
AMRs, on the other hand, do not require any additional infrastructure, such as laser- or wire-guided systems. They do not follow fixed routes, but configure their routes autonomously based on pre-loaded plans of their surroundings. They do this with the help of SLAM (Simultaneous Localization and Mapping). It is mainly the application, operating conditions and logistical planning that determine whether an AGV or an AMR is better suited to the transport task at hand. The VDI Technical Committee AGV has previously released publications with the corresponding definitions. The boundaries between AGVs and AMRs are becoming increasingly blurred. SAFELOG Managing Director Mathias Behounek also has his own view on dividing transport robots into AMRs and AGVs. In his opinion, AGVs and AMRs are technologically almost identical and have more or less autonomous functions. The decisive factor, according to him, is the level of autonomy that best suits the relevant application.
Advantages of driverless transport systems
AGVs and AMRs are used in intralogistics for a variety of applications. Driverless transport systems are highly flexible and adaptable and can take on a wide range of tasks. They are particularly well-suited for automated processes that require speed, precision and reliability.
Other advantages include:
- Increased efficiency: Automated processes can be used to close the staffing gap caused by the skills shortage. Peaks in demand can be absorbed flexibly.
- Relieving the strain on workers: Transport systems take over strenuous, repetitive transport processes, supporting employees in the warehouse and with order picking.
- Continuous availability: DTSs work without taking breaks.
- High adaptability and flexibility: The transport processes are scalable and can therefore be adapted at short notice to suit daily fluctuations or seasonal peaks.
- Excellent process reliability: Strict adherence to processes ensures a continuous workflow. This makes it possible to avoid errors in order picking, material provision and goods transport.
- Enhanced transparency: Defining processes clearly makes it possible to identify potential for optimisation.
- Exceptional health and safety: There are fewer forklift accidents and instances of transport damage.
“Driverless transport systems are highly flexible and adaptable and can therefore take on a wide range of tasks.”
Successfully integrating DTSs
Opting for one mobile robot (and its manufacturer) over another comes down to a number of factors. The available space, the size and weight of the material to be transported, the material flow, and several other aspects must all be taken into account. The requirements for driverless transport systems for automation should be closely analysed in advance. The VDI guidelines 2710 and 2510 contain important information for planning. Safety information can be found in the VDI status report “AGVS safety standard”.
“A key requirement for successful integration is involving employees and specialist departments early on.”
A fundamental requirement for the successful integration of automated transport systems is involving employees and specialist departments at an early stage. In addition, there must be an adequate WLAN signal to ensure communication between the vehicles and the control centre, along with suitable routes. The specific floor type is crucial for safe and smooth material transport, and the routes for the transport vehicles must be kept clean and dry.
Last but not least, suitable peripherals are also crucial, as these ensure the safe and reliable transport of products and components. This applies to both the designated transfer stations for loading and unloading, and any transport aids.
Standardisation and flexibility combined – the new superstructures for DTVs
Custom designs are required to safely transport europallets, meshboxes, euro containers or racks. But how can these be adapted to the requirements of the various DTS manufacturers? With our combination of a standardised base vehicle and customisable superstructures, we offer a smart solution suitable for countless applications. On the one hand, this significantly reduces the project planning outlay for the transport task being automated. On the other hand, it maximises flexibility, as the superstructures (known as Top Modules) can be tailored to the relevant requirements and modified at any time.
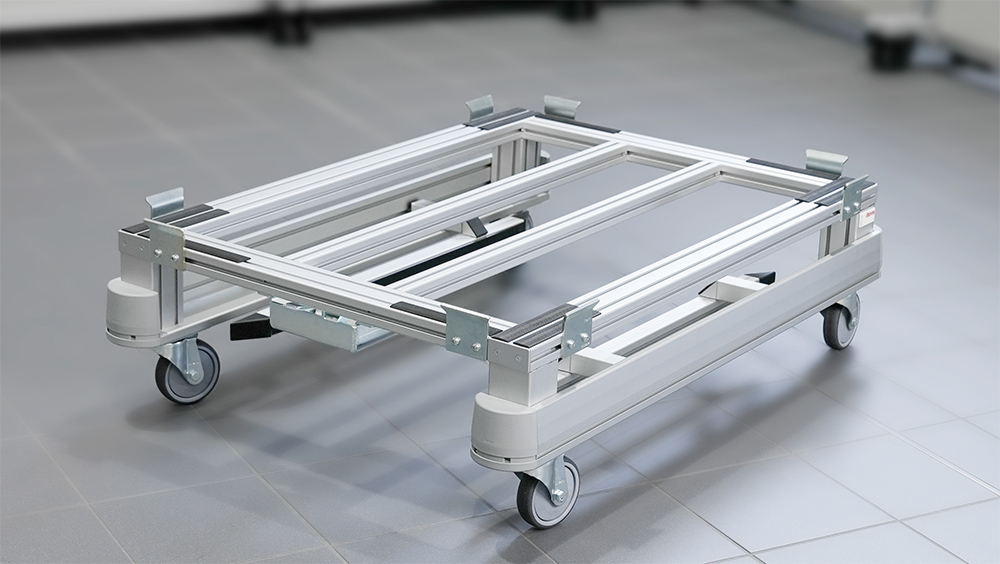
item Base Carts for DTV models from various manufacturers.
Base Carts with Top Modules for a wide range of intralogistics tasks
But let’s go back to the beginning – there are numerous manufacturers of driverless transport systems. The mobile robots differ in terms of their sensors, dimensions and docking mechanisms. Our new transport solution uses a Base Cart as its foundation. This cart is available in various designs and variants, tailored to the precise specifications of well-known manufacturers, meaning that these Base Carts meet the requirements of the vehicle manufacturers perfectly. This ensures, for example, that the vehicles’ sensor technology is not covered and can perform its function safely.
“The combination of Base Cart and Top Modules reduces project planning outlay and increases flexibility.”
A wide variety of superstructures can now be mounted onto the Base Cart. The dimensions of the europallet are the interface between the Base Cart and the Top Module. All Top Modules are designed using the Building Kit System and can be adapted to suit specific requirements. For instance, order picking racks with multiple levels, transport devices for SLCs and complete assembly superstructures are all available. If required, the Top Modules can also be screwed directly onto the mobile robots. What’s more, it is possible to construct fully customised superstructures. “We support the user with carefully conceived solutions that can serve as inspiration,” says Hannes Fröhlich, product manager for robotics at item. “Sample solutions can be ordered directly or fine-tuned in the item Engineeringtool. This means our customers can quickly get a solution for their driverless transport systems.”
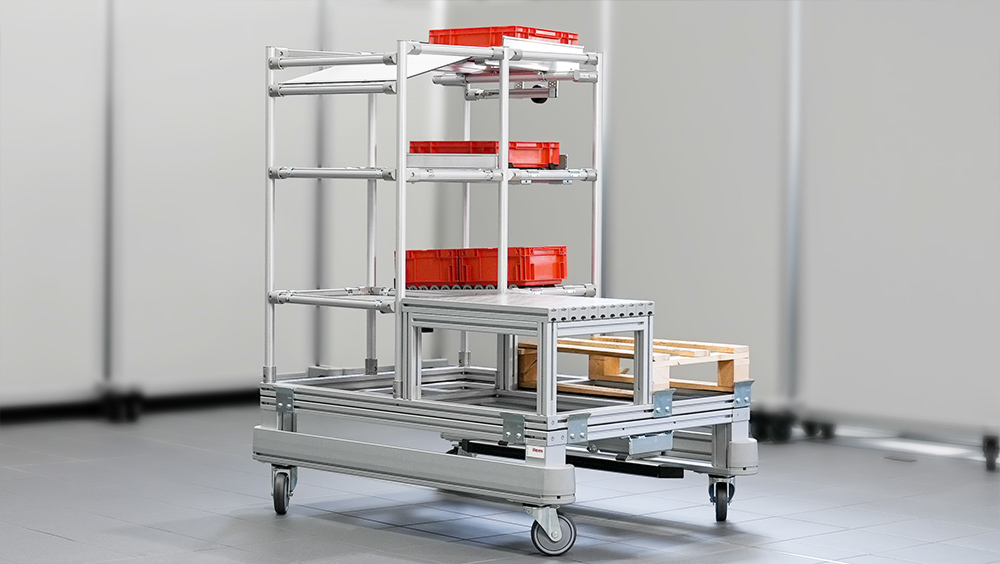
The Top Module is placed directly on the Base Cart and linked to it through a uniform interface. Tailor the Top Module to your particular requirements and processes.