Flexible cobot solutions make a big impression at a vocational college
What is the best way to familiarise classes of students with cobots? One vocational college has come up with an answer – using cutting-edge educational methods and modular robot benches.
Looking back at his own time at vocational college, Benjamin Lange has very clear memories. “We did a bit of programming and the rest had to be drawn out for us, on the chalkboard, for example. Today’s young people come into vocational college, start programming cobots, and get to see the results first hand.” This is a direct consequence of Lange’s own efforts. He works as a design engineer and sub-project manager for automation projects at ibk IngenieurConsult GmbH. This company, which is part of the item pluspartner network, grew up in the automotive industry. It is now increasingly focusing on automation and robotics for small and medium-sized enterprises (SMEs). Thanks to straightforward programming and the ease with which they can be integrated, cobots have become a real success factor for SMEs. These advantages also make them ideal for training the next generation of skilled workers. As a result, ibk is receiving ever more queries from this sector, too. This is how “CobotStreet” came to be created at the BBS-ME (Berufsbildende Schule Metalltechnik • Elektrotechnik der Region Hannover – Otto-Brenner-Schule), a vocational college for metal technology and electrical engineering in the Hanover area.
The profile technology from our modular item Building Kit System provides perfect robot peripherals.
The “CobotStreet” name and the concept for this training facility were developed by the teaching staff at BBS-ME and created in conjunction with ibk. A small project team led by Nils Sternberg was able to secure funding from the German State of Lower Saxony for the concept. The project team focused on creating robust and versatile training benches. Diverse additional modules, such as sensors, racks, conveyor belts, etc., can be attached to the benches to create many different creative tasks that will appeal to a variety of students. The tasks range from very simple jobs (straightforward pick-and-place) to complex problems that require all the robots to work together – which means the students also have to collaborate. The profile technology from our modular item Building Kit System provides perfect robot peripherals.
Integrating cobots into production.
Get to know all the advantages of cobots and the steps for successful integration in the free white paper. Download now and get ready for automation with collaborative robots.
Innovative construction in vocational school for the first steps with cobots
CobotStreet is where the skilled workers of the future gain their first experience with collaborative robotics. The classes of students training for technical careers learn the basics in hackathons, where several teams of up to five people compete against each other to solve a specific task within a defined period of time. With just a few instructions to go on, the teams work towards a solution through experimentation. Cobots from Universal Robots are to grab blocks of wood and place them in a box, for example. It is a fun way for students to learn how to program pick-and-place tasks. The vocational college uses a vision system from OnRobot for automatic image recognition. The company also provides the end effectors used. Other exercises include writing on a whiteboard and simulating engraving by precisely following the contours of letters lasered onto a rubbish bin. After learning the basics, the students consider application scenarios relevant to their own specialisms. “The lessons and the newly gained experience on CobotStreet were really fun, and provided insight into potential new areas of interest,” says Kaan Grigin, one of the students. Based on the positive response, a cross-school hackathon was held in 2023.
The benches can be pushed around by hand very easily. If necessary, you can unplug the power supply, roll up the cable, stow it under the bench and then change location.
CobotStreet provides the perfect platform for these different projects. Five robot benches are grouped closely together. They are around 1 m wide and 1.60 m long. Profiles 8 40×40 were primarily used to build the benches. Profile 8 is the most frequently used of our aluminium profile types worldwide, and is famous for its versatility. The 2 m² table tops offer plenty of space. They are made from a section of groove plates with interconnected profile technology. This solid surface provides continuous grooves and a wide range of options for customised superstructures with smaller constructions for material storage. In addition, the benches can be folded up at the sides to provide additional working space. The cobots are attached to the benches using robot mounting plates. Roller conveyors make it possible to transport material from one cobot to the next. Beneath the table top, there is space for the robot controller and other peripherals. Four fixed castors provide mobility for the robot benches. “The benches can be pushed around by hand very easily. If necessary, you can unplug the power supply, roll up the cable, stow it under the bench and then change location. Once you get to the new location, you can simply plug it in and continue working,” says Benjamin Lange. It is also possible to connect together smaller robot solutions to create a larger application. The different cobots then work together, creating a real “line” or “street” – hence the name CobotStreet.
Practical project for the care sector as a response to the shortage of skilled staff
Another robot application can be connected to the CobotStreet superstructure. In this case, a cobot on an item robot column operates a pass through dishwasher from Ackermann Spülmaschinen GmbH. This is a collaboration with a partner vocational college in the care sector, which is also in Hanover. The BBS-ME and the partner college secured funding for the project jointly. This solution offers an answer to an acute question in these times of skills shortages – what happens when someone is off work and there is no one to stand in for them? “In our solution, the whole thing is automated – the cobot takes over all the worksteps. We have programmed it in such a way that it opens the pass through dishwasher, inserts and removes the trays of dishes, and switches it on again. This is a realistic and everyday scenario,” Lange explains. The practical nature of their training as a whole has been very well received by the students. “Interacting with the cobots was very educational for all the students, and provided a great deal of motivation. It was an extremely positive experience that showed how technology can enhance the workplace. We were grateful to be able to work with such advanced technology at BBS,” says student spokesperson Matthias Bokelmann in summary. He and Kaan Grigin attend “A-class 2023” at the Fachoberschule Technik (FOT, technical college) at BBS-ME.
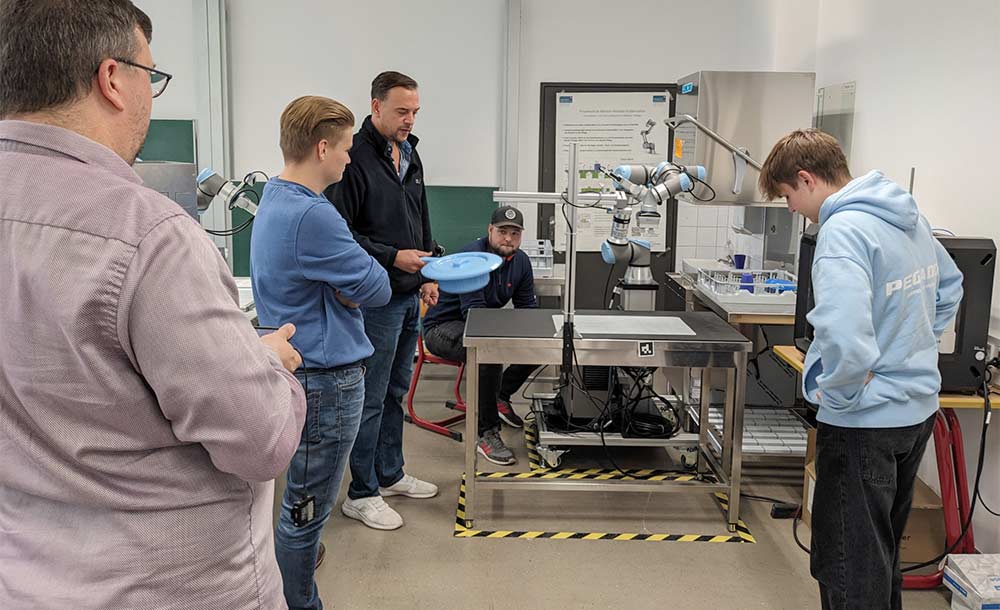
Modularity as a success factor for training institutions
As an item pluspartner, ibk is very familiar with our profile technology. item pluspartners are specialised companies that create customised solutions using item parts and third-party components such as cobots. At ibk, they particularly appreciate the end-to-end modularity of the item Building Kit System. Existing constructions can be flexibly adapted and expanded. Benjamin Lange makes the direct comparison between aluminium and steel: “If we were working with a finished steel construction, that would be really difficult, or even impossible. On an item construction, all you have to do is release a screw and move the components around. This makes life so much easier when you want to try out new things. And when you are done, everything is fastened just as securely as if it were welded.” The flexibility is a huge factor for the teaching staff at BBS-ME. No major investments are needed for new approaches and tasks on CobotStreet. It is easy to fit add-ons to the modular table top. The first ideas for doing just that are already being worked on. Screws instead of welds – this is what enables our modular principle to really take off, especially in training facilities. After all, technical progress never stands still.
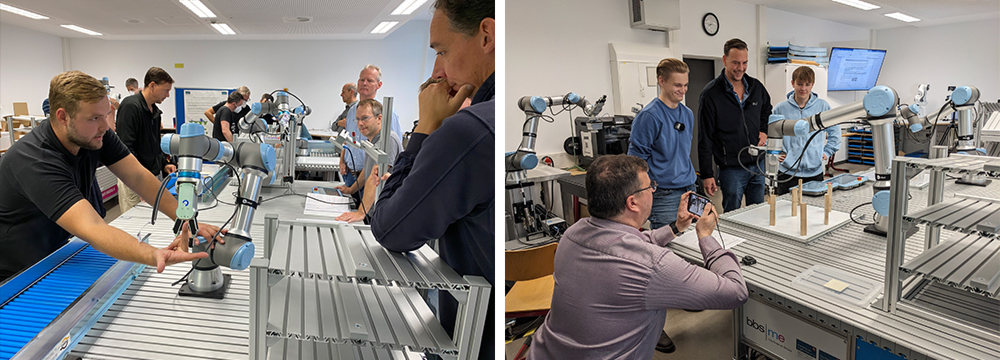