Finding appropriate safety fixtures for machinery and equipment
Familiarise yourself with the basic definitions, distinctions and details relating to safety fixtures.
When people and machines are working together, special safety fixtures need to be installed to ensure these people aren’t in danger at any point. Depending on the circumstances on site, these safety fixtures may be permanent or temporary. A distinction is made between guards and protective devices. Guards can be fixed or movable. In both cases, they prevent personnel from accessing the machine.
Protective devices do not prevent access to the danger zone. If staff approach, the equipment in the danger zone is switched off and production is stopped. Safety fixtures are also used to ensure the safety of machinery. For example, they virtually rule out any tampering with the individual machines. A safety fence is often used to cordon off the machine, and additional warning signs ensure staff work safely. You can use the item Enclosure and Guard System as a protective measure. Numerous item pluspartners will be happy to help you with this. The item pluspartner network covers the whole of Germany and includes a large number of highly specialised companies. It is the perfect basis for projects in all kinds of areas and on every possible scale.
Danger zones and hazards
Occupational health and safety measures must be taken seriously. They serve both to prevent occupational accidents and to avoid work-related health risks for your staff. Especially in the production section, there are numerous hazard areas and hazards. All staff must regularly be briefed about the hazardous situations at their workplace. They should receive instruction on safety and health at work at least once a year and this should be documented, as required by Section 4 of DGUV Regulation 1 (DGUV = German Social Accident Insurance).
“The decision relating to the type of safety fixture is made on a case-by-case basis.”
Whether deliberately or unconsciously, staff often circumvent safety fixtures. With this in mind, you should create additional safety fixtures or precautionary measures in the interests of general plant safety. The decision relating to the type of safety fixture is made on a case-by-case basis. Consider its design in the context of the planned measure. The starting point is the result of a risk assessment based on the Machinery Directive.
What are guards?
A guard is a physical barrier between personnel and a machine’s danger zone. It protects the danger zone from unauthorised access and can take the form of safety fences, safety doors, covers or entire casings. Protective enclosures on machinery (machine enclosures and machine housings) are also ideal, enabling you to stop your staff getting close to the hazard area.
“Guards can be fixed or movable.”
Guards can be fixed or movable. Which option you choose depends on your requirements. Fixed guards are directly connected to the machine. One prerequisite for this option is that the guard does not negatively affect the machine’s productivity. The guard must be permanently installed and cannot be detachable. Removal must only be possible with additional tools and when the machine is not in use. Fixed guards must be made from a particularly resilient material. If necessary, a guard can also be transparent so that the hazard area remains visible.
Examples of fixed guards:
- Walk-in protective enclosure
- Protective enclosure of a cleaning cabin with lifting door
According to DIN EN ISO 14120, you are only permitted to use these guards if regular access does not need to be ensured.
Movable guard
A movable guard is also located between people and the machine’s danger zone, but it can be easily removed without using additional tools. It must be permanently connected to the machine. This type of guard often takes the form of doors in safety fences or hatches at openings. Other examples of movable guards include swing doors and sliding doors.
Examples of movable guards:
- Protective enclosure for a laser marker
- Laser safety cabin for research
- Mobile test stand for burst pressure testing
- Protective enclosure with corner door
According to ISO 14120, you should use a movable guard if you need to ensure frequent access to the hazard source.
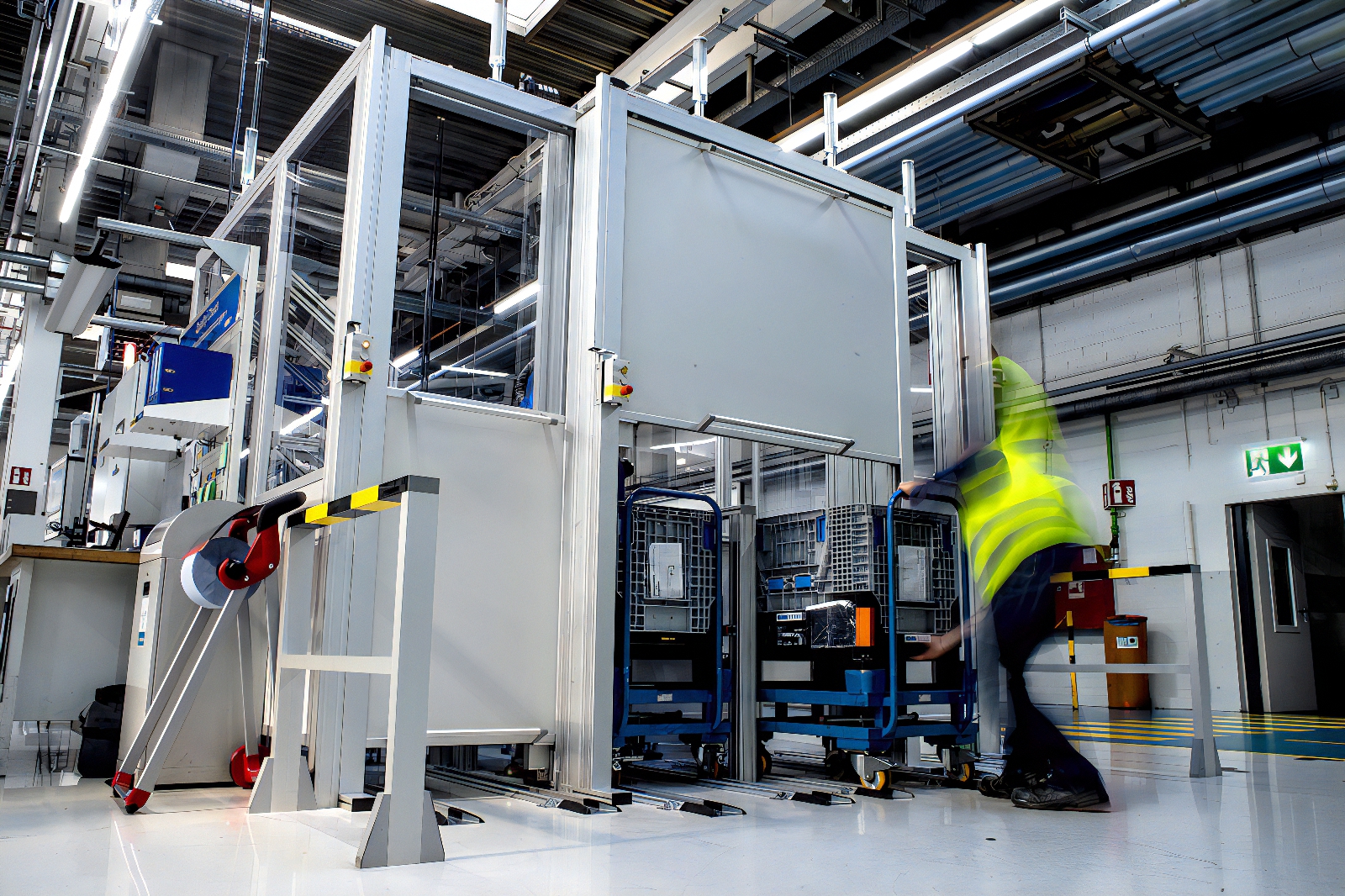
Interlocks as safety devices
In addition to movable guards, you can fit interlocks based on DIN EN ISO 14119. In most cases, the machine is controlled using safety switches. The switch position or the safety device’s interlock shows you whether the machine is operating. If you release the interlock, the machine stops. Staff can then enter the area without putting themselves at risk. One important thing to note is that an interlock does not prevent opening. For this purpose, you should select a type of interlock with locking.
“Locking devices can also be added to doors or hatches.”
On a door, strong electromagnets or springs can be used for this. Before opening the door, you should deactivate the electromagnet or spring. Locking devices can also be added to doors or hatches, meaning the machine will only operate when the door/hatch is closed.
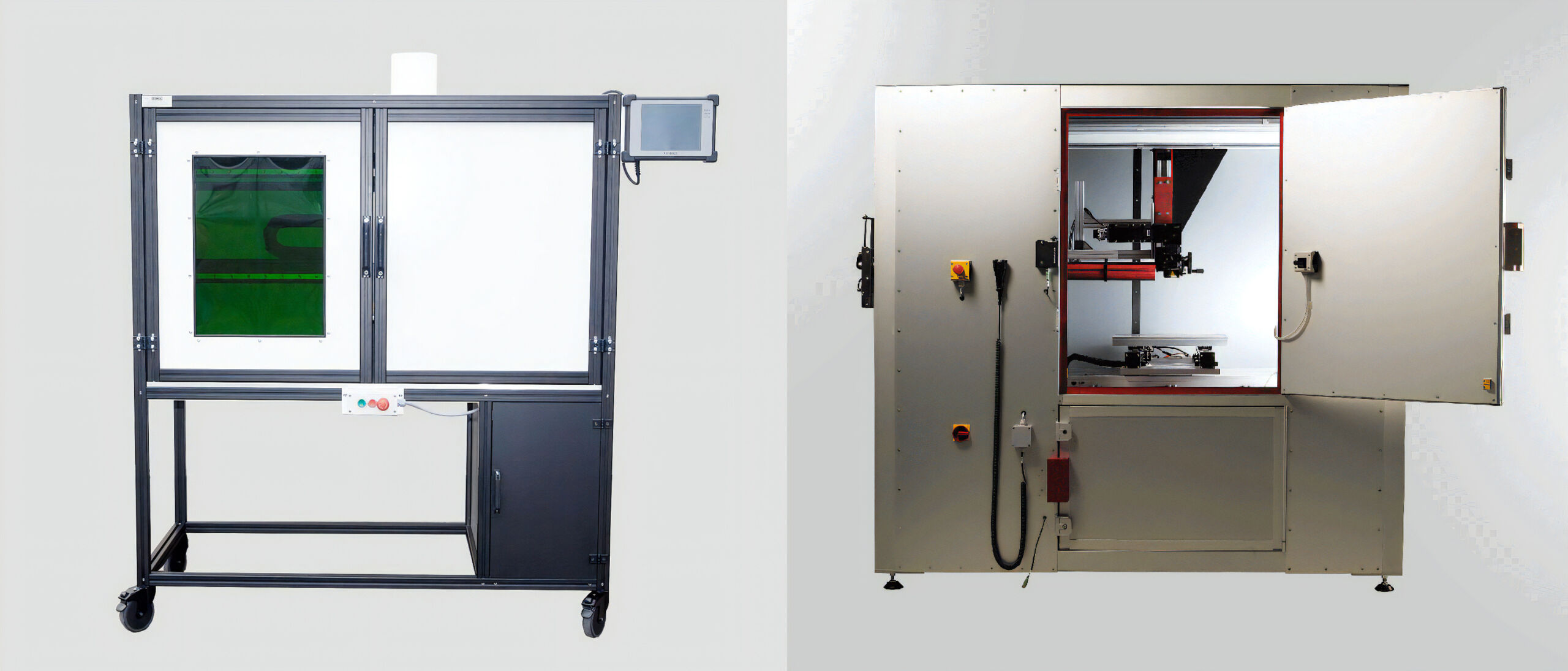
Minimum distances and specified heights for guards
If you are looking to design and build guards yourself, you should bear in mind the requirements relating to materials, types of fixing and minimum distances to hazard sources. Ensure compliance with ISO 13857, which tells you about the necessary safety distances. In other words, staff must not be able to reach hazard sources with their hands, feet, legs or arms.
The minimum distances do not just depend on the location of the hazard source, but also on the person to be protected.
The distance to the safety fixture depends on the environment and the person to be protected. Hazard areas can be accessed by reaching up, reaching over, reaching round and reaching through. The minimum distances do not just depend on the location of the hazard source, but also on the person to be protected, with different measurements applying to people of different sizes. These measurements serve as a guide for you. They are based on a person working in the normal way. Improper use and deliberate circumvention of safety precautions are not taken into account in the standard.
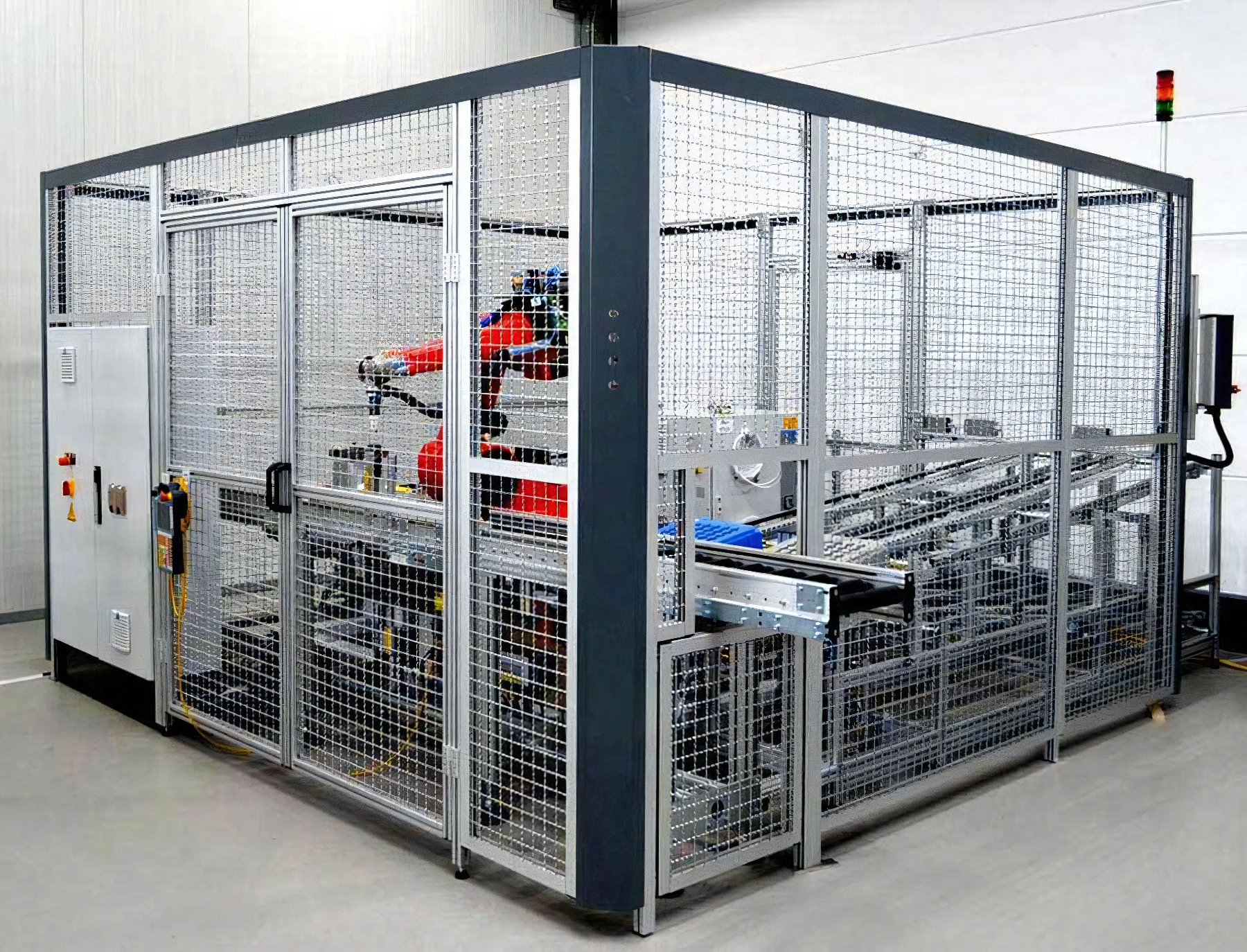
What is electro-sensitive protective equipment?
Electro-sensitive (contactless) protective equipment is used when frequent access to a hazard area is required or when it is impossible to install a guard at the location in question for structural reasons. Protective equipment of this kind is regulated in DIN EN 61496. It protects the area around a production machine. Since protective devices are normally visible, this equipment is also referred to as electro-sensitive protective equipment.
Examples of electro-sensitive protective equipment:
- Light barriers, light grids or light curtains
- Scanners
- Safety shut-off mats
- Two-hand control devices
In the case of electro-sensitive protective equipment, the machine stops when a light barrier is crossed.
In the case of electro-sensitive protective equipment, the machine stops when a light barrier is crossed. A safety shut-off mat works according to the same principle. In the case of two-hand control devices, the machine only runs when both hands activate an operating element. This safety equipment protects the arms and hands of staff. Protecting the machine is of secondary importance.
What are adjustable guards restricting access?
Some work areas need to be entered frequently by certain staff despite being a hazard source. For example, the responsible staff need to be able to operate a circular saw. You can use an adjustable guard restricting access to protect the danger zone. Your qualified staff can then easily access their workstations. At the same time, you create a clear barrier between them and the personnel outside the danger zone.
Tampering with safety fixtures and protection against starting up (again) unexpectedly
It is not uncommon for safety fixtures on machinery and equipment to be tampered with. There are many different reasons for this. Staff often hope to gain an advantage by doing so, without considering major drawbacks such as serious accidents, machine stoppages and higher operating costs. The manufacturer of a safety fixture is the person to talk to when it comes to improving the safety of personnel. Ideally, this manufacturer will have a solution to ensure even better protection.
Some machines can start up unexpectedly. This can also happen automatically.
Some machines can start up unexpectedly. This can also happen automatically. You must therefore never enter the danger zone of such machines if they do not have a restart interlock. This interlock is one of the machine’s safety fixtures. The two-hand system is often used. A machine can then only be started if both hands move to a different position. This type of machine safeguard ensures the machine cannot be switched on accidentally.
Are emergency devices essential on machines?
Generally speaking, a distinction is made between two safety concepts – emergency stop and emergency shutdown. An emergency stop is when the machine is stopped in response to an emergency. In other words, all dangerous movements are brought to a halt as quickly as possible. In an emergency shutdown scenario, the machine should shut itself down completely. In this case, the machine must be disconnected from the power supply. The risk assessment is carried out on a case-by-case basis. You need to ask yourself whether the emergency device is required for the safety of machinery or people.