Basics, design tips, components, and sample solutions – discover cleanroom technology with item.
Dust particles that are just 0.5 µm in size cannot be seen with the naked eye. The abbreviation “µm” stands for micrometer – that’s one thousandth of a millimeter. To put things into perspective, human hair has a diameter of 40 to 120 µm. Don’t be fooled by seemingly innocuous dust particles, though – they may be harmless in normal, everyday life, but their presence can have extremely serious consequences in hygiene-sensitive industries and the manufacture of certain products. In some ways, it is similar to protection against electrostatic discharges (ESD) – special solutions are required to shut the door on an invisible danger. Specifically, cleanrooms are what is needed in this case. For example, ISO 5 permits a maximum of 3520 particles 0.5 µm in size per cubic meter. A typical living room might contain as many as 35 million particles per cubic meter. However, how does a cleanroom cut the number of particles down so far? How does it actually work? What are the key aspects of cleanroom design? And what really matters when it comes to working in a cleanroom? Join us as we take a tour through the world of clean production. We are always at your side – this is another area where the item building kit system ensures customized, flexible solutions.
System solutions for cleanrooms
Use the modular design principle to create safe cleanroom solutions! Whether you need a work bench with laminar flow box, a cleanroom cabin or a partial enclosure, item will help you implement solutions in exactly the dimensions required.
What is a cleanroom? A simple explanation
According to ISO 14644-1:2015, a cleanroom is a space where the number of airborne particles is kept to a defined, low level. To this end, the room must be designed, built and operated in such a way that the amount of particles brought into the room, or created or deposited there, is reduced. A cleanroom is needed whenever products and processes need to be protected from contamination. That means complying with specific limits. In this kind of controlled environment, it is possible to clean the air in a targeted way. In some cases, other parameters such as temperature, humidity and air pressure must also be controllable. This is another way of creating standardized conditions within a room. Fundamentally, cleanrooms are used for work in the semi-conductor, optics, electronic, optoelectronic, IT and processor technology industries, among many others, including the automotive, food and pharmaceutical sectors. Aerospace engineering also relies on cleanroom technology. The term “cleanroom” does not always necessarily refer to a closed room that you can walk into. It can just as easily be used to describe small process enclosures with clean conditions. These special solutions are also known as “mini environments”.
The specific circumstances of the relevant production environment dictate any further steps. What matters now is which class of cleanroom you need. That will define the requirements for specific processes in the cleanroom. Cleanroom classes are defined in two different guidelines – ISO 14644-1 and GMP guidelines. These are also the core guidelines for cleanroom technology. You must also comply with other standards and specifications, some of which are industry-specific. ISO standard 14644-1 focuses on preventing particles building up in the air. It is therefore relevant for technical industries, including semiconductor production and the plastics and automotive industries. In contrast, the GMP guidelines focus on pollution from micro-organisms. This makes them the primary guidelines for cleanrooms in the pharmaceutical industry, medical technology and sterile production. When it comes to the limits for airborne particles, GMP classes A to D are based on ISO cleanroom classes 1 to 9.
Significance of airflows in cleanrooms
Fundamentally, cleanrooms are based on the following principle: In a specially designed environment, overpressure (to protect the product) or underpressure (to protect the environment) is created. In overpressure environments, filtered – and therefore clean – air is generally fed into the space from above. Depending on the requirements of the cleanroom, a low-turbulence displacement airflow or turbulent dilution or mixed airflow can be used. In a low-turbulence displacement airflow, or laminar airflow, the air is fed into the room across the entire ceiling surface in as even and smooth a way as possible using fan filter units. This pushes the air already in the room downwards, so it can leave the room at close to floor level, thus ensuring that abraded particles and fine dusts are not stirred up, which would damage sensitive areas of a cleanroom. In turbulent dilution or mixed flows, on the other hand, the filtered air is fed into the cleanroom in a turbulent state, for example using a ventilation plate. This continuously dilutes the particle concentration. As a result, there is no need to cover the entire ceiling with fan filter units.
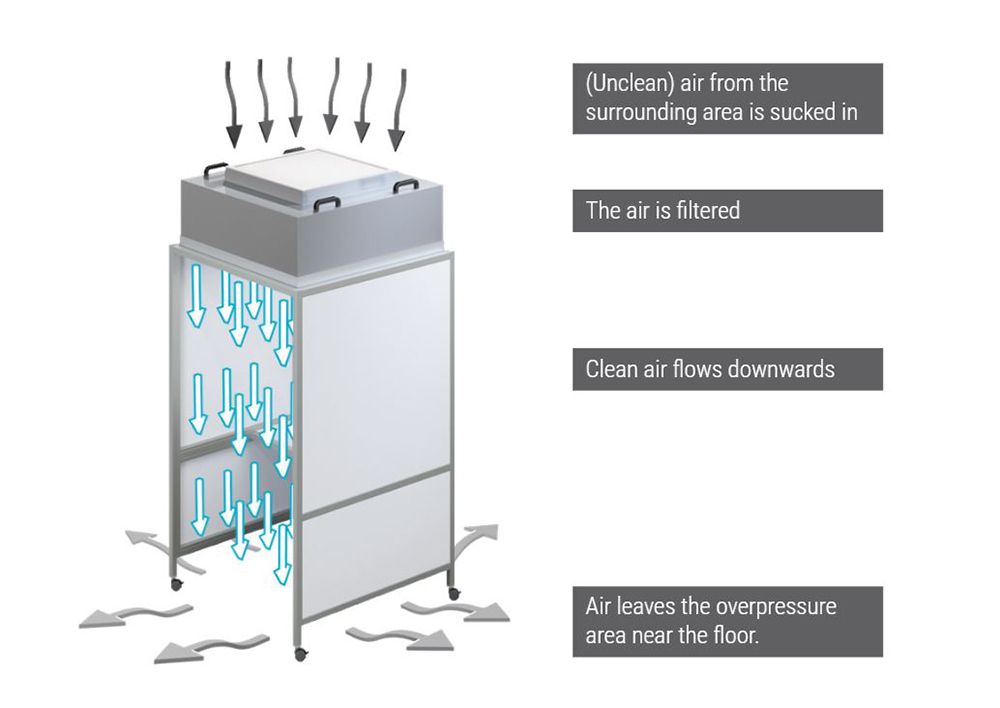
Different types of cleanroom
There are different cleanrooms to suit different requirements. A filter fan unit (FFU) is installed above a single cleanroom work bench, where it generates a low-turbulence (laminar) airflow. The particles within the cleanroom are thus forced directly downwards, where they can escape close to floor level. You can also design machinery as a cleanroom – either completely or partially. A clean process housing makes it possible to keep the cleanroom as small as possible. As a result, only the sensitive process is conducted under cleanroom conditions, cutting the outlay for cleaning and monitoring the air as far as possible. If your products need to be manufactured under particularly clean conditions, you can construct your cleanroom using a room-in-room concept.
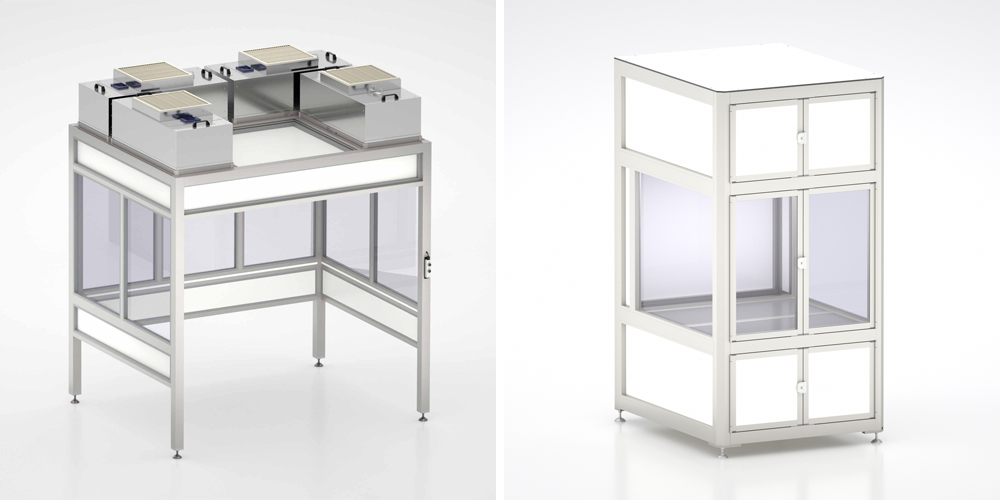
Partial cleanroom enclosure (left) and a clean process housing (right) for comparison.
Optimized cleanroom design – components for walls and ceilings
The specific requirements determine the components needed. Frequently, simple elements are enough for cleanroom production, including ceiling constructions and wall and side elements, for example. For the latter, you can choose between a softwall partition (vertical blinds) and a hardwall partition (panel elements). Fixing System X 8 is available as a basis for forming walls and ceilings in cleanroom production. Flush, easy-to-clean transitions and the modular design make it possible to use Fixing System X 8 wherever an area needs to be cleanly closed off from the surrounding environment. Compound Material HPL 36mm is suitable for panels in a sandwich design. The “HPL” (high pressure laminate) designation says it all – during production, numerous layers of paper or cellulose fiber are pressed together with binders under high pressure. HPL panels are smooth, easy to clean and resistant to cleaning agents. The panels are fully enclosed between Profiles X or XMS without having to be machined in any way.
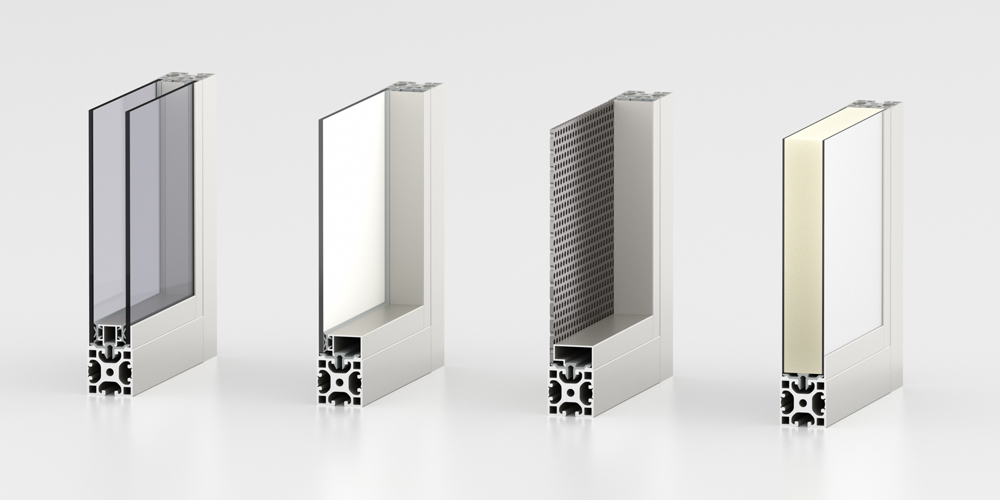
These images illustrate the flush-mounted, modular panel installation options that Fixing System X 8 makes possible.
Air for keeping working and process environments clean!
A filter fan unit (FFU) is required to clean the ambient air. A pre-filter and HEPA filter form a single unit with the FFU housing. Our Filter Fan Unit removes 99.995 % of all particles from the ambient air thanks to its HEPA H14 main filter. In other words, only five airborne particles in 100,000 get through an H14 filter. The pre-filter stops larger particles. FFU Housing 1200×600 serves as the basis for the filter fan unit. At its heart is a fan that draws in air in its upper section. Air is fed carefully through the sound-proofed housing to the primary filter. By fitting your item solutions with integrated return conduits, you can achieve air quality that is almost entirely independent of the environmental conditions. This will also extend the service life of the filter.
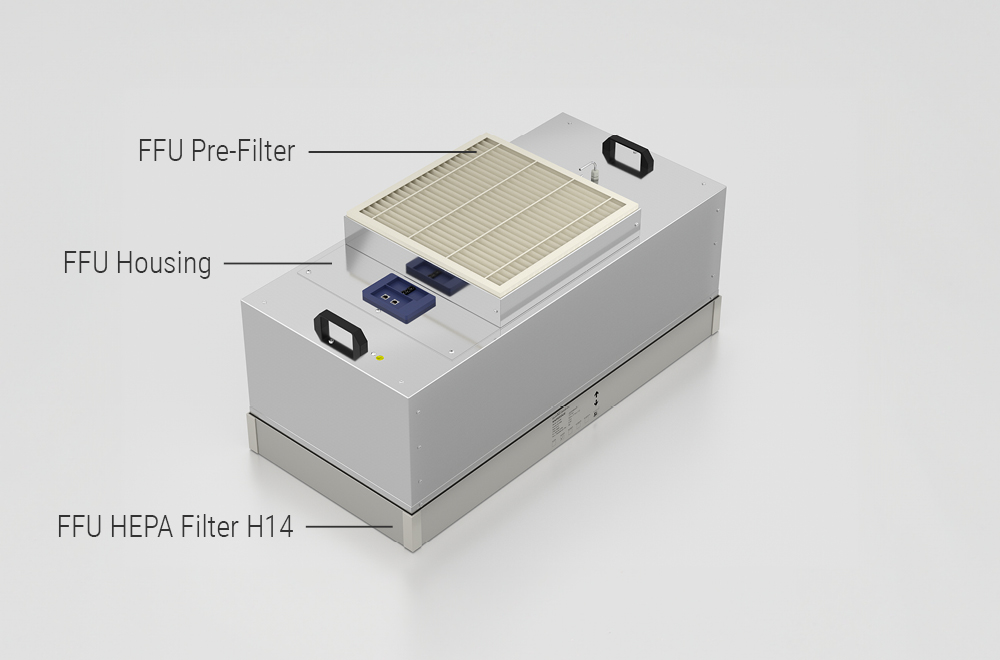
Whether stationary or mobile, you should use our cleanroom-compatible aluminum Profiles X or XMS for your base frames. Their properties include:
- Small edge radii
- Only as many open grooves as necessary
- Easy cleaning
- Resistance to cleaning agents
Whether laminar flow boxes, ergonomic cleanroom work benches, process and partial enclosures or walk-in cabins and enclosures, our components make it possible for you to create customized solutions for working in a cleanroom. Qualified partners from our network and our Customer Solution Sales team will be happy to help.
Modular solutions for cleanroom technology
You will find a range of sample solutions for cleanroom applications available in the item Online Shop. Thanks to complete CAD data and parts lists, you can use these exactly as they are. With the laminar flow box with height-adjustable work bench, you can manufacture products efficiently and ergonomically at a work bench under cleanroom conditions. The solution can generally be certified up to ISO class 5. Obtaining such a certificate of compliance is a long, drawn-out process. The ISO classes are influenced by other factors (such as the type of airflow and how well sealed the cabin is). The specific design is therefore decisive. Using a stainless steel Perforated Sheet as the working surface ensures that the low-turbulence displacement airflow in the flow box can be routed away without it swirling around. Pivot Arms from the item Work Bench System can be added to supply materials and tools as required.
You can also use the laminar flow box as a table-top unit. This laminar flow box offers variable use of space for a work bench in a custom size. You can configure the hood complete with filter fan unit as a flexible table-top unit that is only used in production when absolutely necessary. Just like the work access opening, it can be adapted precisely to the production process. The machine cabins with the Filter Fan Unit and air recirculation are based on Line XMS profiles. You benefit from integrated cable conduits and easy-to-clean unbroken surfaces. The Filter Fan Unit generates a high-purity laminar displacement flow that passes through the work area and reaches the lower level through a perforated sheet and is fed back to the FFU via the rear wall. Thanks to this clean environment, the solution qualifies for certification to cleanroom class ISO 2.
Rules of conduct when working in cleanrooms
However, there is more to cleanroom production than setting up a safe work bench. Human beings are one of the primary sources of contamination in cleanrooms – their breath and particles from their clothing and skin alone can cause up to 40 percent of the contamination. As a result, there are particularly stringent demands for cleanrooms and specific rules of conduct for staff. Depending on the requirements of the cleanroom class, protective clothing may need to be worn while working, such as gloves, masks, hair nets, full hoods, overalls and overboots. Alongside cleanroom clothing, how each individual conducts themselves in the cleanroom is vital. Fundamentally, only specialist personnel with the relevant training should work in cleanrooms. Hurried movements while working represent a risk factor that may seem surprising at first glance. However, these can shed and swirl up comparatively large numbers of particles. Staff at these work benches should therefore move slowly.
What’s more, you should keep the number of people in the cleanroom to a minimum. This is another way of releasing fewer particles into the air. The rules of conduct also forbid bringing food and drink into the cleanroom and consuming them there. Jewelery and other personal items have no place in a cleanroom, either. Even make-up is not permitted inside a cleanroom, as it contains particles that can settle on the work bench surfaces. Better safe than sorry – if employees feel ill, they should not enter a cleanroom, even if they are wearing protective clothing. Coughing and sneezing can have terrible consequences, including contaminating the cleanroom. This is another parallel to ESD protection – in cleanrooms, too, success comes through a combination of equipment and conduct. We would be delighted to help you with both of these factors through our modular building kit system and our expertise, which we are happy to share.
Want to keep up to date with everything that’s going on in the world of item? Simply subscribe to the item blog by completing the box at the top right.