Focus on automation – conveying technology at KM Packaging
The lids go here, the cannulas go there – components and products are transported automatically in the KM Packaging production facility. Conveying technology from item delivers efficient processes and smooth operations.
Open up to every challenge – that is the motto of KM Packaging GmbH. The company specialises in sealing solutions and is facing up to the challenges of the industry. Efficiency in production is the basis for continuous growth. Whether tube and bottle closures, cannulas, jar lids or customised packaging, KM Packaging produces over 6.5 billion injection-moulded parts annually. Globally, it supplies renowned customers in the tube industry and major brand manufacturers in the cosmetics and pharmaceuticals industries. The company has almost 500 employees working at six sites in Germany, Austria, Poland and the USA.
At the heart of item conveying technology – the Conveyor Belt System
Find out more about the item Conveyor Belt System. This overview will tell you everything you need to know about flat belt conveyors, timing belt conveyors, motors, gearboxes and accessories.
Using the Conveyor Belt System for automated processes
KM Packaging has been using our components for decades already, in a large number of their production areas. The packaging specialist has now also discovered item conveying technology. “The rapid and international availability of its components is just one of the reasons we chose item,” says Tobias Kamuf, Project Manager Plant Planning/Automation at KM Packaging GmbH. “After all, we use the Conveyor Belt Systems in our production plant in Hebron in the United States, too.” What’s more, the packaging specialist intends to use systems predominantly from a single manufacturer in the future, so as to reduce interfaces to a minimum. An additional advantage is that item has a very comprehensive portfolio of mutually compatible components, making it possible to construct just about anything. When it comes to automating its assembly and packaging processes, KM Packaging has therefore once again opted for item products, including several Double Timing Belt Conveyors and Flat Belt Conveyors in various lengths and widths.
“The rapid and international availability of its components is just one of the reasons we chose item.”
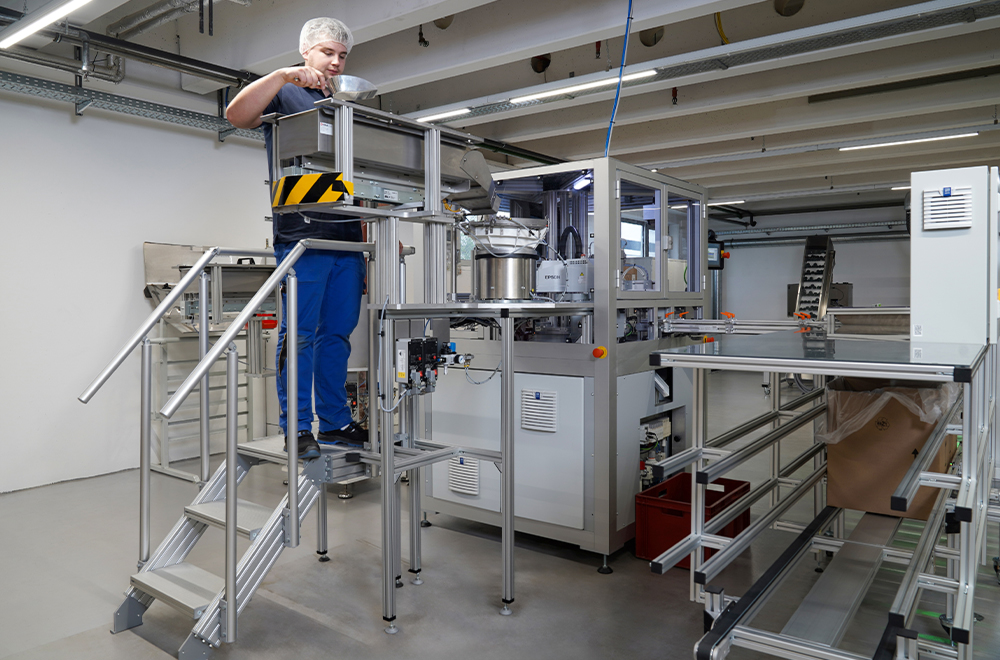
Optimising assembly processes with item
The rotary indexing assembly system is a great example of the wide range of potential applications for our components. This uses an automated production process to manufacture a special closure consisting of three parts – a cannula, a threaded ring and a cap. Various conveying systems take these plastic parts to the rotary indexing assembly system. The cannulas, for example, are transported using the item Flat Belt Conveyor, on conveyor belts 80 mm wide. The finished piece is transported to the filling station on another Flat Belt Conveyor. The filling station is constructed using our profiles and fasteners. The rotary indexing assembly system has been integrated into a machine cabin made from Line XMS profiles. Integrated cable conduits and special seals to protect against dirt and dust are just two of the many advantages of these high-performance machine modules. Their unbroken outer surfaces also make them very easy to clean. The sensitive assembly process is perfectly protected against external influences as a result. Our Stairway/Platform System is also used in the assembly process to provide a climbing aid for when a container attached at a height of two metres needs to be refilled.
Filling station made from item components – including conveying technology
After leaving the rotary indexing assembly system, the finished closures are transported to the filling station. Empty cartons measuring 600 mm x 400 mm also make their way there on Double Flat Belt Conveyors with belts 80 mm wide. Once the empty carton is correctly positioned, the filling process starts automatically. The loose, finished closures fall from the Flat Belt Conveyor via a buffer element into the carton until it contains the required quantity. The filled cartons then continue their journey on conveyor belts or roller conveyors from item and are prepared for shipping.
KM Packaging is thrilled that the portfolio of components and fasteners – which was already huge – has now been augmented to include numerous variants and designs of conveying technology. “We can get everything we need to carry out automated projects with this degree of complexity from item – from individual profiles and the feet of base frames to panel elements made from special materials,” emphasises Tobias Vowinkel from KM Packaging’s technical management/die-making team. Since the constructions are made of aluminium profiles and matching fasteners, and can be modified quickly and simply, they can be adapted to suit new requirements perfectly. This put KM Packaging in a position to implement the automated assembly and packaging processes much more easily than if they had been working with a welded structure, for example, that is rigid and offers far less flexibility.
The rotary indexing assembly system is a great example of the wide range of potential applications for item components.
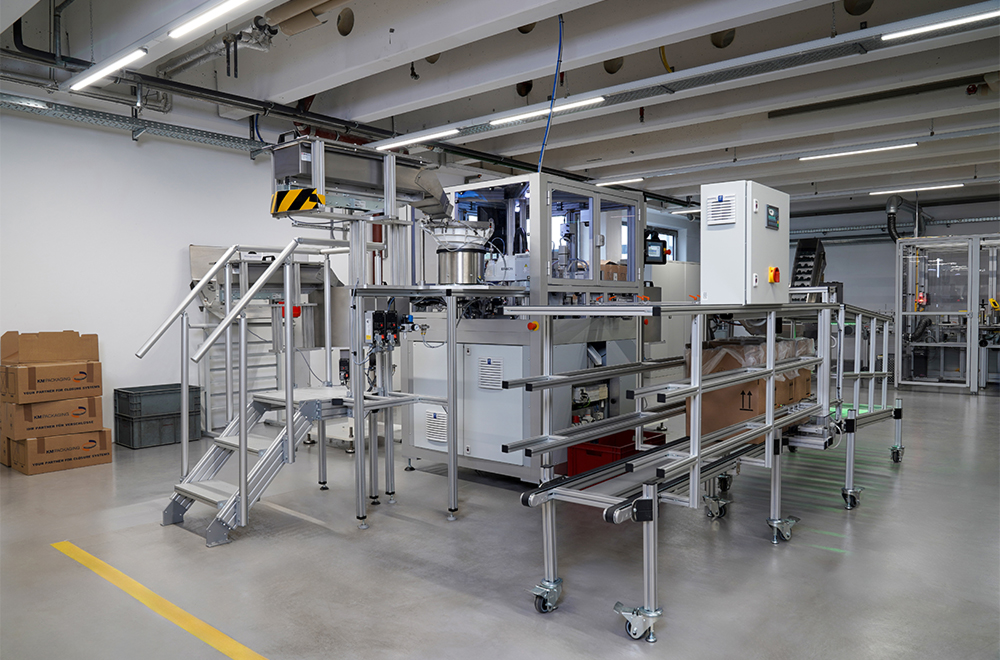
Digital support rounds off the portfolio perfectly
The Engineeringtool offers valuable support when it comes to configuration and design. All basic models can be adapted to the on-site circumstances quickly and easily in this way. What’s more, it is possible to combine the Conveyor Belt System with other systems, such as the Work Bench System. The benefits of the tool include the option to design custom configurations directly in your browser, comprehensive documentation including parts list, the requisite CAD data, and much more.
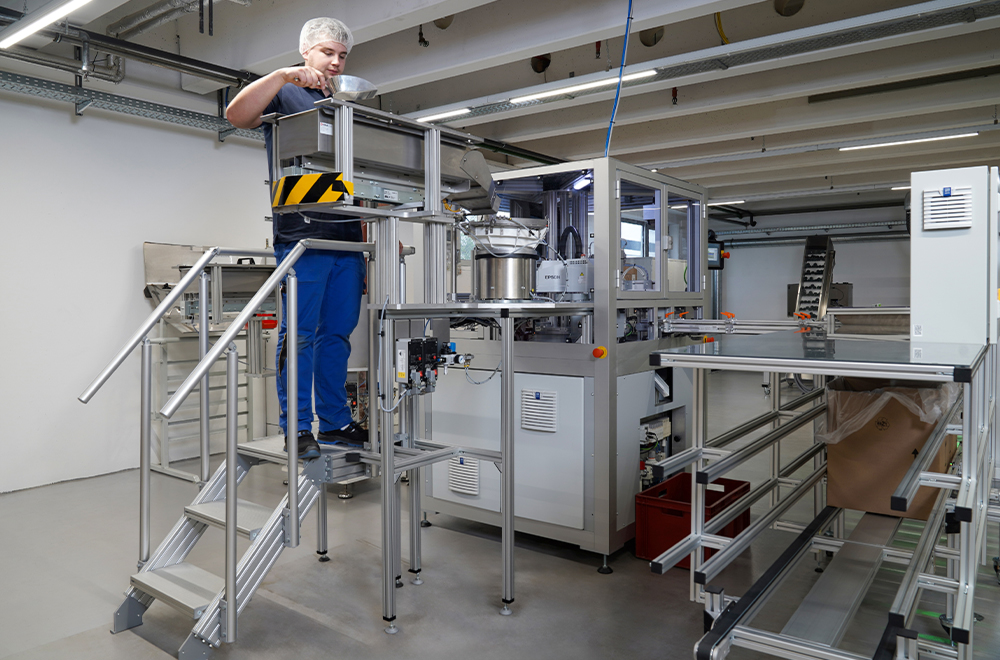
Whether it be climbing aids, conveyor belts or machine cabins – the modularity offered by item means everything can be combined flexibly. As a result, ideas for new projects almost create themselves.
Perfectly equipped for future challenges
The Building Kit System, with its modularity and flexibility, and the optimum support from item employees are reasons enough for KM Packaging to plan and implement more projects in partnership. Just recently, for example, a new assembly system was created based on the profiles, and a labelling machine is currently in the planning stage. The frame and conveying technology in the new machine are also set to be created using our components. “The item system makes it exceptionally easy for us to add components such as sensors, even after commissioning. Components of this kind are quickly screwed into the system groove instead of having to be laboriously installed, as is the case when using conventional systems,” says Vowinkel. This makes item products perfect for complex, automated assembly and packaging processes. Since the collaboration is also working perfectly, there are no more obstacles in the way of a successful working relationship in the future. KM Packaging is therefore perfectly equipped to face the challenges of the future.
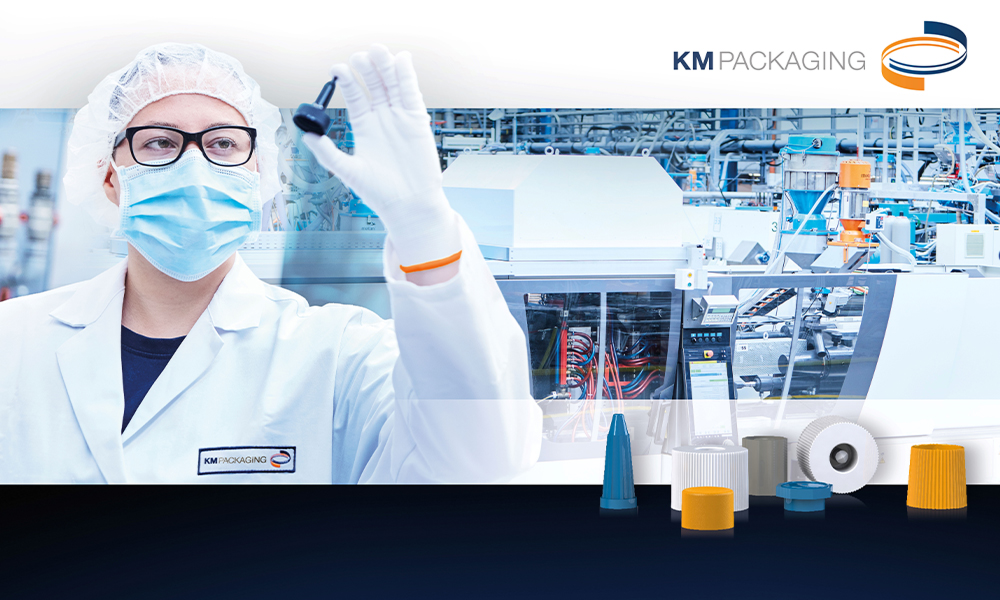
KM Packaging has decades of experience in injection moulding and boasts one of the most cutting-edge machine parks in the field of closure solutions.