When it comes to boosting the efficiency of industrial work benches, ergonomics are often overlooked, according to work bench expert Marius Geibel from item in this interview.
However, companies can achieve three benefits at the same time: Eliminating uncomfortable movements boosts efficiency and motivation – and lowers illness rates.
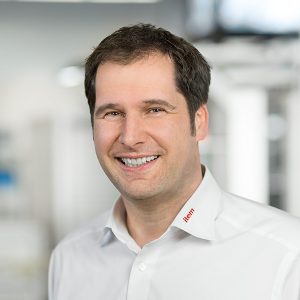
Marius Geibel, Product Manager
The term ergonomics covers a lot. Why should companies engage with it?
Health and safety is a legal requirement. But that shouldn’t be the biggest motivating factor. Ergonomic work benches can save time, reduce error rates and lower sickness rates. Companies that want to do the best that they can, should engage with this concept.
Ergonomics sounds like it’s about making things comfortable for employees. Is it about making people feel better?
Ergonomics is often seen as an unnecessary and costly way of trying to turn the workplace into some kind of health spa. However, in a holistic approach, improving productivity is an integral aspect of ergonomics. In practical terms, ergonomics and efficiency go hand in hand.
Personnel who are not under unnecessary strain are more motivated and perform better. Ergonomics helps companies to retain their workforce for the long term and find effective solutions for dealing with the demographic changes that are causing so much debate. Employees benefit from better health, and companies benefit from better efficiency. It’s a win-win situation.
Ergonomics boosts efficiency? How can that be proven?
Eliminating superfluous, unnecessary and uncomfortable movements saves on time and strength. The best example to take is the movement of goods inside a company. Manual production requires a supply of materials – without waiting times. If materials can be conveyed to personnel without any high edges and heavy lifting, the whole process runs faster and involves less strain. That is referred to as ergologistics – a combination of ergonomics and logistics.
Work benches should be compatible with a range of logistics concepts, such as changing from individual assembly islands to continuous flow production as appropriate to product requirements. When using a modular work bench system, companies can utilise benches, transport trolleys and roller conveyors very efficiently over a long service life, without putting unnecessary strain on personnel.
Can specific figures be put on the benefits of ergonomics? Is there any hard evidence?
Most effects are long term, but that also means they are all the more sustainable. It isn’t easy to corroborate the benefits of ergonomics with absolute precision because individual factors can’t be separated out like they can in laboratory testing. The study “Vorteil Vorsorge” (Prevention Pays) that was conducted by Booz & Company on behalf of the Felix Burda Stiftung foundation used the results of a survey to arrive at a return on investment of at least 1 to 5. No financial investment brings returns like that. Ergonomics pays.
How difficult is it to design work benches to be ergonomic?
That all depends on how well established ergonomics already is as part of the company’s corporate culture. Often, small steps can have a big impact. Besides lowering days lost due to illness, ergonomic improvements virtually always optimise processes. If you start to ask the right questions, you won’t necessarily need huge refits to have a discernible effect. There are practical guidelines that are easy to follow and will ensure companies take ergonomic principles into account when designing workstations.
How can you actually tell whether a work bench system is ergonomic?
Ergonomics isn’t a product, it’s the culmination of a whole host of measures. It usually makes more sense for companies to bring in an expert to carry out a professional assessment. There are good solutions for that, such as Ergolyse from item, which combines an analysis of the current situation with specific suggestions for improving ergonomics and processes. Institutions such as Aktion Gesunder Rücken e. V. (AGR, the Campaign for Healthy Backs) also offer good guidance by recommending equipment and aids that have been independently certified, such as ergonomically optimised work bench systems.
Combined sit/stand workstations have long been a feature of the “office world”. Can this same method be applied to industrial production?
Of course, it can – production personnel can benefit from exactly the same advantages. Wherever processes allow, employees should be able to change between sitting and standing as they do their work. Height-adjustable work benches make that possible.
Isn’t it impossible to have a bench that is both stable and adjustable?
Stability is fundamentally important in production but, with the right drive solutions and linear guide technology, there is no reason why height-adjustable work benches should be in any way limited.
Which areas still pose risks for health and efficiency? And how can an ergonomic work bench system help in those scenarios?
In an industrial environment in particular, a lot of the work that is done involves manual operations that are repeated over and over. Employees have little choice in what posture they adopt and that quickly leads to the development of painful constrained postures. That makes employers all the more responsible for ensuring that, wherever possible, work is adapted to people – not the other way around.
It is crucial that the systems for providing personnel with materials, tools and information, the lighting at the work bench and so on can all be tailored to the physical characteristics and abilities of the worker. By using a building kit system to design a work bench, I can tap into virtually unlimited options for adapting equipment to personnel and the production process.
Are ergonomic work benches automatically suitable for disabled users?
Not necessarily. Ultimately, disabled employees merit special attention to ensure their cognitive or physical limitations are taken into account. When using a modular work bench system, I naturally have a lot more freedom to do that than when working with “standard” equipment. When it comes to inclusion, the same applies as everywhere else: People are the most valuable asset any company has.