The coronavirus pandemic saw the demand for masks skyrocket. Meeting that demand meant finding solutions fast.
The demand for medical face masks has risen particularly steeply. These are not the everyday fabric or “community” masks that keen crafters around the world are now churning out. Although such face coverings do lower the risk of the wearer passing on the coronavirus to others (source control), they fall short of the stringent requirements in medical and industrial environments, where the wearer needs to be protected from infection and/or pollutants. Surgical masks – a type of medical face mask – provide more effective source control than community masks but still offer the wearer only limited protection. By contrast, a respirator, or filtering face piece (FFP), without a valve provides effective source control and protects the wearer from the coronavirus, too.
Naturally, governments across the world are keen to access supplies of high-quality masks without having to rely on imports. This is where Jonas & Redmann Group GmbH comes in, a company that specializes in automating complex production processes. In next to no time, the specialist mechanical engineers developed production systems for manufacturing certified FFP2 masks and surgical masks. The company is using Line XMS from item to build the enclosures for its production systems, and both machine types can be supplied in an impressively short space of time.
Fully-Automated Production Line for FFP2 Masks and Surgical Masks
Specialist mechanical engineering projects on this scale usually take around eight months to complete. However, since the basic principles of mask production are very well known, the team had a solid basis to build on: “We looked into the general state of the art so we could improve it in very specific ways and build in our design approach. We worked fast – compressing about eight months of work into eight to ten weeks,” says René Klärs, Head of Assembly Automation at Jonas & Redmann.
The production system Jonas & Redmann Group GmbH built to manufacture FFP2 respirators without valves can turn out up to 150,000 masks per day, depending on the type being made. To achieve this output, material is fed into the system and processed in sync. Everything is fully automated, from feeding in and applying the nose clip, shaping the mask contour and welding on the headbands (both using ultrasound) to compression, straightening the headbands, separation and stacking the masks. A special spunbonded nonwoven fabric is incorporated into the centre of the masks and features an antistatic charge, which prevents coronavirus particles from penetrating. The second, fully automated system for manufacturing surgical masks is also designed to produce masks at high speed.
XMS profiles from item are the basic elements used to build both production lines. Their benefits were clear to the specialist engineers, since closed grooves make these sturdy profiles very easy to clean – a crucial consideration in medical engineering. It was also particularly important that the system should have a high-quality look, too. All in all, Jonas & Redmann have come to appreciate item as a dependable partner over the course of a long-standing collaboration, as Klärs reports: “We have been using item for more than 30 years in all sorts of systems. They range from small standalone frames to large series production lines.”
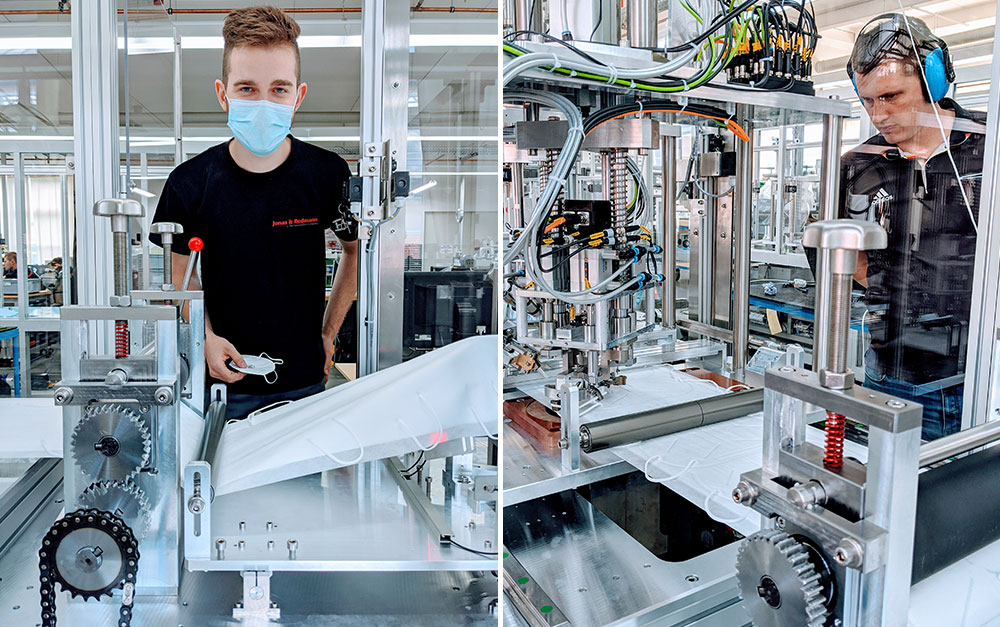
Different Customers, Same Goal – Making Masks
The production lines for making masks are aimed at three different types of customer. Firstly, there are the large companies, where there is no doubt that making masks for use in in-house production is worthwhile. This safeguards their independence and enables them to supply their staff with masks they have made themselves. “The customer can start running their machine as soon as they take delivery. As with all our machines, system operation is geared towards the user,” explains Klärs. Secondly, there are companies that have been commissioned directly by the authorities to manufacture masks. They will either already be operating in a related area, such as textile manufacture, or they will have already built up trust with politicians.
Thirdly, there are companies that normally operate in a different field but have switched to mask production either to develop a second mainstay or due to current demand. In all three cases, quality, service and speed are critical factors. If a customer wishes to manufacture standard masks, the whole process from ordering through to delivery of the production system takes just eight weeks or so. The delivery time for custom solutions is correspondingly longer. For instance, customers may have specific requirements regarding the nose clip or the design of the headbands that require modifications to the standardized production system. However, one thing applies to all system variants: “We naturally use tested materials. The masks made on our machines guarantee certified protective performance. Our customers can rely on that 100 percent, even if additional customer-specific requirements are being implemented,” declares Klärs.