How companies can ensure continuous improvement in production.
The continuous improvement process is the bedrock of lean production. However, achieving continuous improvement requires more than simply rolling out or implementing a new process. While having to think things through makes progress slow, the opposite is true when acting intuitively – if you get the hang of something in a carefree way, you do it faster. It is only when certain principles have been fully internalised that they can become habits and then ultimately an established part of corporate culture. But what methods can be used to achieve this kind of effect? In the lean production context, there is the KATA method developed by Toyota. This term is taken from Japanese martial arts, where exercise routines are practised constantly until they become ritualised and can be carried out without thinking. When it comes to lean production, there are two distinct kinds of KATA – the Improvement KATA and the Coaching KATA. In the first part of our KATA series, we are looking at the Improvement KATA.
The Improvement KATA is lean and exceptionally structured
One of the key differences between the Improvement KATA and conventional procedures for improving processes is that the former specifies the target situation. This helps avoid unstructured discussions, prevents experiments without a plan and stops individuals taking on too dominant a role. Instead, it is possible to get closer to the target situation through structured discussions and a scientific approach. Specifically, the Improvement KATA builds on the following four steps:
1. Understand the challenge
2. Establish the current situation
3. Define the next target situation
4. Use PDCA to experiment and get closer to the target situation
The first step is about identifying an overarching challenge. This is particularly important as it highlights the significance of each individual target situation – however many they may be. Establishing what the current situation is involves a dedicated process analysis. This might go as follows:
1. Output performance
What output does the process generate over time?
2. Customer takt time and planned cycle time
How fast should the process operate?
3. Process properties
Create a block diagram of the workflow
Measure the cycle time with spread
Record your own observations
4. Factory equipment capacity
Does factory equipment capacity impose any restrictions?
5. Number of employees required (if the process were stable)
How many workers are needed?
Using the Improvement KATA to enable employees
Let’s go back a step. What exactly is a target situation? This refers to the process properties and KPIs you would like to achieve. Let’s take an example from the world of sport: “How the game is played” takes precedence over the actual outcome of the game. After all, you can directly influence how free throws are taken in basketball, but you can’t directly influence a specific desired outcome (e.g. 80 percent of free throws). In addition, we have to rethink how we use Return on Investment (ROI). Usually, ROI helps define a target economic situation. It is therefore used to determine where we are going. Toyota uses ROI in a different way. The company defines its destination beforehand (without ROI). In the context of the Improvement KATA, ROI only serves as a measure of how this previously defined target situation will be achieved economically.
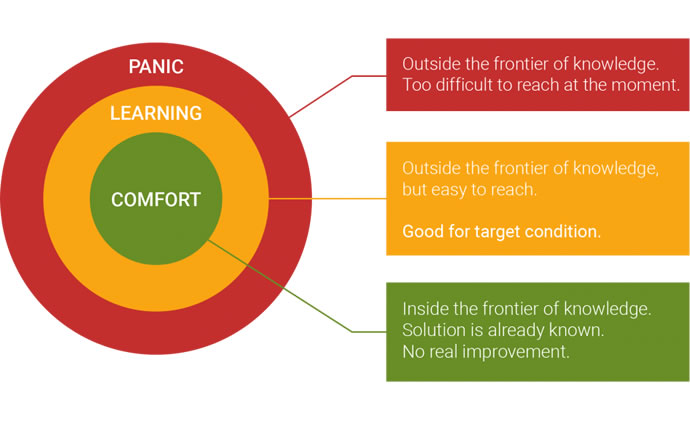
The target condition should be outside the frontier of knowledge and inside the learning zone.
There’s no such thing as an entirely smooth path, however. An essential element of the Improvement KATA is drawing up a list of specific obstacles. Experiments are conducted on how to overcome these, such as new approaches in production. However, this doesn’t mean every obstacle has to be moved out of the way, so this isn’t a list of strictly specified measures.
Here’s how to experiment using the PDCA method:
1. PLAN
Hypothesis/prediction: What will be done and what will happen?
2. DO
Conduct the experiment, observe and measure.
3. CHECK
Compare the prediction with the outcome of the experiment.
4. ACT
Assessment: Standardise what worked.
Short, fast, hands-on experiments enable you to quickly expand the boundaries of your own knowledge. For example, when using Profile Tube System D30, frames can be easily modified without complex reworking or special tools, and it’s a one-person job.