The field of robotics covers much more than just industrial robots and cobots. For example, mobile transport robots offer a genuine advantage by taking over time-consuming intralogistics tasks.
Using AGVs or AMRs to automate transport tasks in intralogistics is a key step in easing the strain on staff. What’s more, material transport is one of the seven types of waste (muda) in lean production, a production philosophy that considers any activity that doesn’t add value to be waste. After all, moving materials from place to place ties up important resources. By automating repetitive tasks such as these, companies can free up their staff to focus on the real work that generates value. Moreover, there is a pressing shortage of staff in the intralogistics sector. As a result of all these elements, mobile transport robots are becoming an increasingly common feature in intralogistics operations – both in industry and in eCommerce. The robots being used can often be categorized into two types – AGVs and AMRs. So what are the key features of each robot type? What are the main differences between them? And to what extent do these distinctions ultimately help a company decide on which type best fits its needs?
Automated guided vehicles (AGVs) – ideal for fixed routes and excellent reliability
Automated guided vehicles (AGVs) come in various shapes and sizes, for example to fit under trolleys, specialist superstructures or trailers, or to push or pull loads in a role similar to that of automated forklift trucks, tractors and lift trucks. In German-speaking countries, a distinction is made between a “driverless transport vehicle” (fahrerloses Transportfahrzeug or FTF), which is the individual vehicle and a “driverless transport system” (fahrerloses Transportsystem or FTS), which is a complete system comprising AGVs and a control station. The biggest distinction between an AGV and an AMR is its method of navigation. Unlike an AMR, an AGV is restricted to a fixed route. Although it can identify obstacles, an AGV can’t drive around them, and instead stops and waits until the obstacle has been removed. Fundamentally, an AGV therefore needs a special infrastructure that incorporates markings such as magnetic tapes, wires, QR codes or reflective markings.
Given the need for this additional infrastructure, any changes to the production environment and processes have a knock-on effect that results in extra outlay. However, the procurement costs for AGVs are usually lower than for AMRs, which use technology that is more complex, making them more expensive on the whole. AGVs do require some initial outlay for setting up the environment, although this is not necessarily a disadvantage. The key to deciding between an AGV and AMR is what the specific transport task and scenario require. For instance, if your scenario centers on routes that don’t change, or only change very little, and involve a low number of obstacles, then an AGV could prove more cost-efficient than an AMR. The tasks and routes of AGVs also ultimately end up being simpler and clearer than in the case of AMRs, which benefits their dependability and safety. Their routes and behavior are a fixed, known quantity, which means staff know how best to act around them. They are particularly popular in the automotive industry. For example, Audi uses a combination of AGVs and supply trolleys built using item profile technology in the manufacturing operations for the Audi A8.
Autonomous Mobile Robots (AMRs) – especially flexible and versatile
Autonomous mobile robots (AMRs) have attracted particular attention in industry over recent years. The word “autonomous” indicates primarily that an AMR is not allocated to one specific route, but can instead adapt to its surroundings in real time. This adaptability is based on maps that are either uploaded to the system or are generated by the AMR itself. Using integrated cameras, scanners and sensors, the AMR automatically calculates the shortest route to its destination. If it encounters obstacles, for instance, this flexibility means that it doesn’t have to come to a stop and can instead find and take the best alternative route. If there are changes to its surroundings or if new working processes are introduced, the AMR can therefore adjust to them with ease. As they are not tied down to markings, there is no additional outlay associated with adapting routes. At the same time, AMRs cost more than AGVs because they utilize more complex hardware and software components, although their improved operational capabilities can offset these costs. All the same, it is always important to carefully consider the situation at hand.
Older distinctions between AGVs and AMRs have often emphasized that the latter are only suitable for transporting lightweight loads. Although AGVs do still have a slight advantage in this regard, special AMRs are now available that can transport payloads of up to 1350 kg. In contrast to AGVs, there are no lifting variants, although AMRs can also be fitted with a range of add-on modules and rack superstructures. For example, as part of an in-house project to optimize intralogistics in its European logistics headquarters, item developed two special constructions – a base frame made from the MB Building Kit System for the MiR250 AMR from Mobile Industrial Robots (MiR) and a rack superstructure, 90 percent of which is made up of components from the Lean Production Building Kit System. Having been successfully tested and put to regular use, these solutions are now available to item customers, too. Both constructions can be adapted to different MiR models and transport tasks. This is where the item Engineeringtool comes in very handy, as this example of a rack superstructure shows.
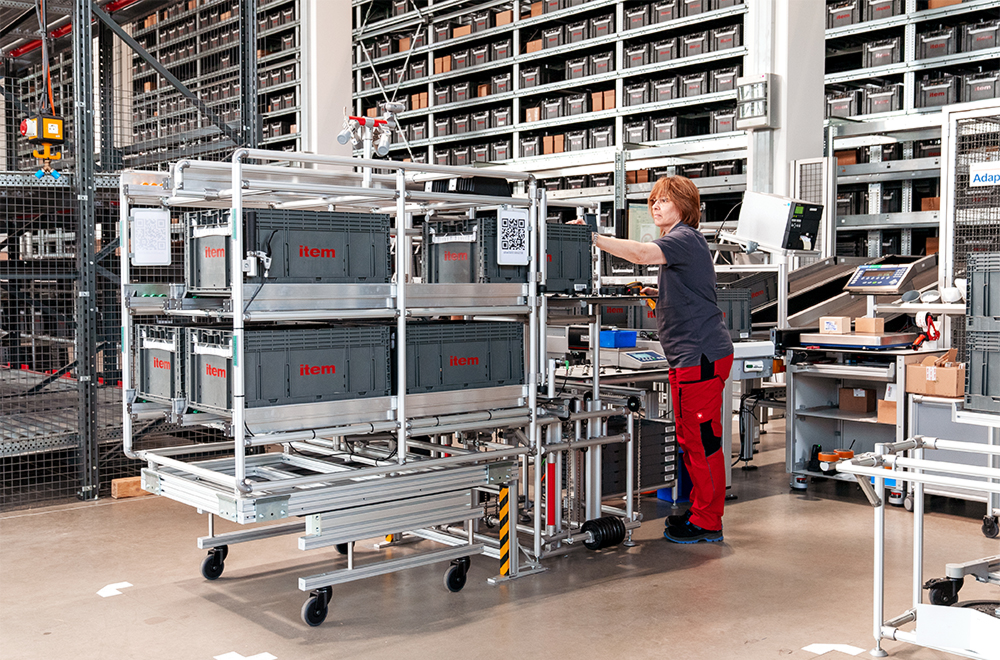
A staff member loads materials into the rack superstructure while it is on the base frame, then summons the AMR, which automatically docks and carries the load to its destination.
All About Autonomy – AGV, AMR, or mobile robot?
According to the team at MiR, AGVs are being challenged by the more sophisticated, flexible, and cost-effective technology of autonomous mobile robots. While AGVs and AMRs both move materials from one place to another, that’s where the similarities cease.
An AGV is able to navigate, guided by wires, magnetic strips or sensors, a predetermined and fixed route. If an obstacle should come up in its path, the AGV will detect it but be unable to navigate around it.
In contrast, the capability of an AMR’s navigation is comparable to a car with a GPS and a pre-loaded set of maps. When the car is taught the owner’s home and work addresses, it generates the most direct path based on simple positions on the map. This is similar to the way the AMR is taught locations to pick up and drop off parts. Using data from cameras and built-in sensors, laser scanners, as well as sophisticated software for obstacle detection, the AMR focuses on efficiency when finding a route to its target. Working completely autonomously, the AMR will safely maneuver around forklifts, pallets, people or other obstacles – thereby ensuring that material flow stays on schedule and optimizing productivity.
This high margin of flexibility makes AMRs more appealing to companies facing large production bottlenecks, with adaptability key for adding new production cells or processes. Add in that, traditionally, an AMR is typically a less-expensive solution compared to an AGV, the quick deployment with low initial costs and no costly disruption to production key to expansion for businesses.
Modern Manufacturing: Looking Forward
Modern manufacturing environments have become proving grounds for flexible technologies. With the compatibility of item Building Kit Systems and both AGVs and AMRs, how will you explore implementation in your facility?
Interested in the latest updates in innovative robotics applications? Simply subscribe to the item blog by completing the box at the top right.