From in-house innovation project to practical customer solutions for autonomous mobile robots – that’s called a win-win situation!
Mobile robots will become increasingly popular. This is the forecast of consulting company logistics iq. Specifically, the company predicts the market for automated guided vehicles (AGVs) and autonomous mobile robots (AMRs) will surpass the 18 billion US dollar mark in 2027. Particularly in intralogistics, it is worthwhile relieving employees of time-consuming, monotonous tasks, so they can concentrate on work that creates value. Autonomous mobile robots (AMRs) are playing an increasingly important role in this. They navigate using maps that can be uploaded or generated with the help of the robot. They do not rely on markings (on the floor, for example), instead using only their integrated scanners, cameras and sensors. As a result, AMRs are able to respond flexibly to obstacles and find their way to their defined destination autonomously.
Find Your Robotic Solution
The options are nearly endless. Discover MiR-compatible racks, Karakuri systems, and more on the item Solution Center.
Achieving more efficient working processes with AMRs and item profile technology
Continuous improvement is at the heart of lean production – and right from the outset, the same could be said of item. Every day, Przemyslaw Krzysztyniak, project manager and innovation manager for robotics and automated guided vehicle systems at item, looks for ways of optimizing processes at the various sites. The idea is to combine the item Building Kit System with different robot technologies. “The aim of these activities is to create processes that are as lean as possible. We then test them out in our own intralogistics and assembly facilities. Of course, the later usability of the solutions for our customers also plays a key role,” says Krzysztyniak. These activities are something of a tradition at item. Even the very first aluminum profiles were initially used successfully in the in-house specialist machinery at item. Only when customers noticed them for themselves and expressed an interest did they become an actual product.
The layout of the European logistics center forms the background to the current project for integrating MiR autonomous mobile robots. The center consists of 11 halls and is 225 meters long, so many transport tasks involved long distances. There was therefore plenty of potential to use leaner, more ergonomic processes to make life easier for staff, boost efficiency and cut costs. The spotlight fell on the following intralogistics processes:
- Transporting cardboard boxes and packages that are destined for the post on pallets or in mesh crates – six to nine times a day
- Transporting the small parts in containers for solutions that were designed using the item online configurators – once or twice a day
- Transporting small parts in containers for the assembly of customized solutions – two regular deliveries a day, usually as many as three on request
Previously, all these transport tasks were carried out using forklifts and pallet trucks that had to be operated by employees. These staff members were called away from their real work in order to take care of the transport tasks. There was therefore a need for a solution that would leave these employees more time for their actual jobs and contribute to the ergonomics of their work. In terms of hardware, the decision was quickly made to use autonomous mobile robots from MiR. “It is a very interesting and innovative company. There had already been contact, and we had provided MiR with solutions that they had tried out. We then discovered that the new MiR model is an ideal starting point, so we began developing an application,” says Krzysztyniak. A mobile base frame made from profiles from the MB Building Kit System provides the basic structure for the MiR 250 to dock onto. Depending on the specific task, pallets, mesh crates or even specially developed item racks are attached to the base frame.
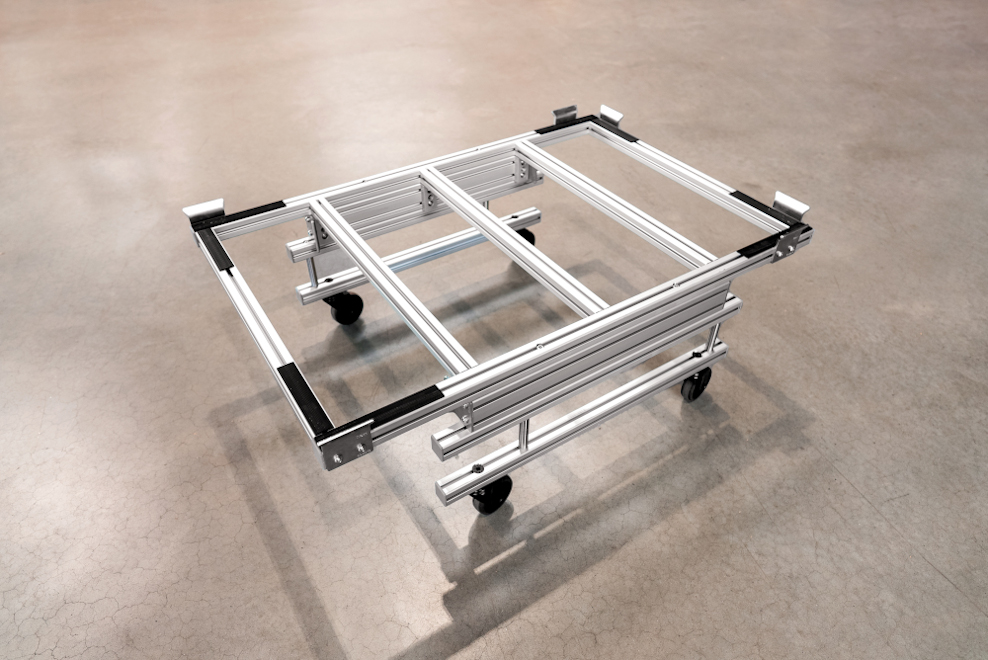
The MiR autonomous mobile robot docks onto this base frame. item racks, pallets, and mesh crates are placed on top of this.
Custom modification of base frames and racks for autonomous mobile robots
Around 90 percent of the rack components come from the Lean Production Building Kit System. As a result, they are incredibly lightweight, robust and easily modified. One particularly practical feature is that the modular construction means both the base frame and the racks can be custom modified. “It is simply in line with our philosophy of developing adaptable standard solutions. While this may sound like a contradiction in terms initially, it is exactly what makes the modular system from item so good,” explains Christian Thiel, who is a product manager and expert for online tools at item and was therefore deeply involved in the AMR project. The item solutions for the MiR autonomous mobile robots were all designed using the item Engineeringtool. There is one big advantage to this – designs can be called up in the Engineeringtool, customized, and then ordered directly.
Although the template for the base frame is designed for the MiR 250, the flexibility of the item Building Kit System and the item Engineeringtool means it is easy to adapt it for other models. Since the length of the profiles can be selected freely in the item Engineeringtool, it only takes a few seconds to adapt the online design to another MiR model. Specific requirements in terms of the weight of the load can be factored in by selecting the appropriate profiles. For example, lightweight profiles are suitable for transporting cardboard boxes or small load carriers (SLCs). When it comes to mesh crates full of heavy parts, on the other hand, particularly strong profiles are required. Similar principles apply to the racks on the base frames. “We defined a standard rack that can be equipped in a customized way. After all, every company has its own applications and requirements. This standard rack can be modified as required – for example in terms of the profiles or the number of roller conveyors,” says Thiel. The first potential customers have already looked at the AMR solutions in action in Solingen and are interested in using them in their own companies. You can order the base frame straight from item. Alternatively, you can simply design your own structure in the item Engineeringtool. You can find our own solution as an example here.
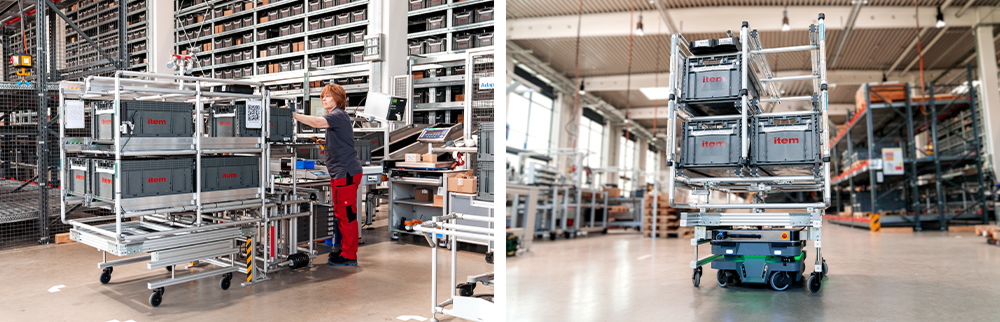
All the employees have to do is fille the rack (left) and the AMR takes care of the transport (right).
Employees’ openness to new directions as a key to success
The example of how small parts are delivered to the hall where customer solutions are assembled demonstrates clearly what a difference the optimized transport processes in the logistics center make. The employee who is responsible for picking the small parts is at an ergonomic work bench or an ergonomic transfer station. The mobile rack has been parked in front of this. She scans the material required and loads up the rack with the SLCs. “The AMR is summoned to the press of a button. It goes under the rack, docks, and then drives autonomously to a parking position in the hall for assembling the customer solutions. That is a journey of more than 200 meters. The AMR deposits its load at the specified position before picking up an empty rack from another station,” Krzysztyniak explains. The AMR then takes this new rack back to its starting point, ready to be filled again. All this creates a cycle in which the AMRs take care of all the transport tasks, saving the staff a lot of time, which they can then spend on their actual work. At the same time, however, this is not full automation. Similarly to human-robot-collaboration, it relies on the employees who have to interact with the AMRs being open to this and accepting this way of working.
Przemyslaw Krzysztyniak appreciates the openness of the intralogistics team towards new technologies and approaches. “The staff on site are the most important link in the chain. You can create the best system in the world, but it won’t do you any good if it isn’t accepted. At item, things are generally very well received. Everyone supports these innovation projects – and sees the benefits for their own work.” The AMR project is currently continuing apace. For example, a rack replacement for the mesh crates is in development. The team is also experimenting with simple automation using shooters. item is now an official MiRGo partner, meaning its solutions for the MiR ecosystem can be found on a special platform. We therefore wait with bated breath to see what further innovations will arise from combining item and MiR.
Interested in the latest updates on innovative robotics applications? Simply subscribe to the item blog by completing the box at the top right.