Perfect teamwork with a non-human colleague is no longer a pipe dream.
Collaboration between human workers and robots is one of the most innovative new developments associated with digitalisation and Industry 4.0. A huge amount of progress has been made with ideas that seemed more like science fiction just a few years ago. At the same time, however, this glimpse of what work might be like in the future raises a number of questions. How exactly does coordination between humans and robots work? And just how compatible are Industry 4.0 and ergonomics? Henning Petruck, a research assistant at RWTH Aachen University’s Institute of Industrial Engineering and Ergonomics (IAW), specialises in human-robot collaboration – a form of cooperation in which humans and robots work hand in hand without any barriers between them. A postgraduate from the “Internet of Production” excellence cluster funded by the German Research Foundation (DFG), Petruck is using a specially designed workplace based on the item Work Bench System to investigate how robots can make life easier for assembly staff.
Working flexibly and ergonomically
The basic idea behind the Collaborative Workplace for Assembly (CoWorkAs) is for a robot arm to pass components and tools to the worker, which makes it a true human-robot collaboration centring on physical contact with a robot. “The worker can focus entirely on the value-adding aspects of production. There’s no longer any need to go looking for all the necessary parts. They just need to be assembled,” explains Petruck. This is made possible by a frame structure with four columns that links a height-adjustable work bench and the material supply and picking system. Two overhead linear axes are connected to the robot arm.
With the exception of this arm, the entire workplace is made of item solutions, including additional elements such as tool and monitor holders. It goes without saying that ergonomics played a key role in the project management team’s choice of service provider. “Following a discussion with item at a trade fair, the company devised a concept for us. We really liked its flexibility, modularity and adjustable height,” says Petruck. The entire workplace is connected together and is fully adjustable to the size of the person using it. What’s more, the modular design means it can be continuously expanded.
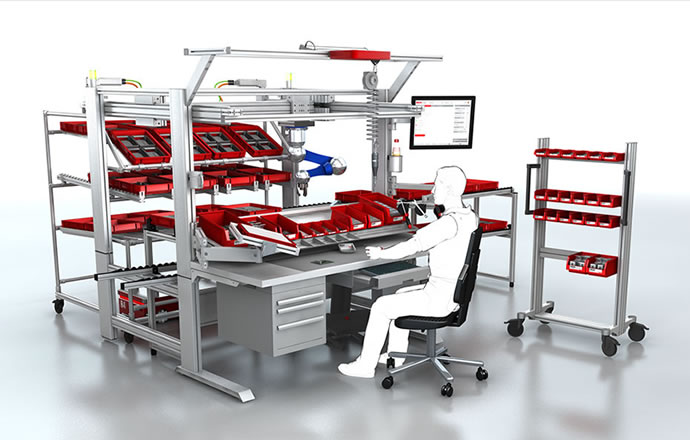
the worker can focus entirely on value-adding aspects.
Human-robot collaboration with perfect timing
The robot arm picks up the object and moves towards the worker. The closer it gets, the more slowly it moves so as to avoid accidental collisions. Moreover, the robot comes to a complete standstill just before reaching its human colleague. This is also important to ensure workers feel at ease, reaching out to take hold of the object rather than having it thrust at them. “It’s a completely new experience for someone to work with a robot – especially when it’s not fixed in place and has a large range of movement, as in our setup. It can be a little disconcerting, and such factors need to be taken into account,” underlines Petruck.
Any human-robot collaboration presents a key technical challenge – how to accurately predict human behaviour. In the case of CoWorkAs, activity detection during the assembly process is used to analyse the time workers take to complete assembly steps. Once the system has observed the first run, an algorithm calculates the difference between the planned and actual time required. “This difference can be used to accurately predict the duration of the next assembly step, which serves as a basis for ensuring the robot arm can pass the component at the right time,” explains Petruck. Passing it too soon would cause the worker unnecessary stress, and the robot would not be available for other tasks.
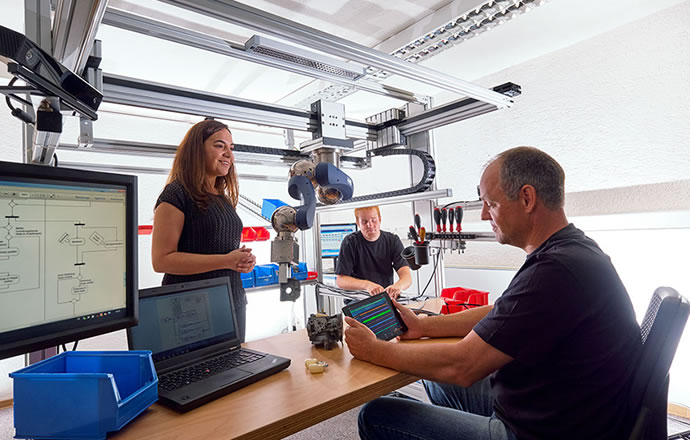
teamwork is deemed very important at the institute of industrial engineering and ergonomics. photo: ahrens + steinbach projekte
Data protection and further research
Any data protection concerns are unfounded with this type of human-robot collaboration because there is no need to save user profiles. The algorithm only requires a few details to adapt to the current user. One run is all it takes. What’s more, upcoming research will be looking into human control of the robot arm. This is linked to work being done by another member of the university’s research team who has developed a control system for paraplegics who can only move their head. Thanks to a head-mounted accelerometer, they are able to control a robot using nothing but head movements. CoWorkAs is to take these experiments to the next level.
For further details, see the paper entitled “Human-Robot Collaboration in Manual Assembly – A Collaborative Workplace”, on which three ergonomics experts from item also collaborated. Professor Verena Nitsch, Head of the Institute for Industrial Engineering and Ergonomics at RWTH Aachen University, and Henning Petruck are also happy to answer any questions.
Are you interested in digitalisation and what the future of mechanical engineering holds?
Then we have something that might just help!
Simply subscribe to the item blog by completing the box at the top right!