From grippers and sensors to base structures – robot peripherals are a broad field. In this post, we shed light on a complex topic. Find out why you should opt for modular solutions when it comes to your base structures and other peripherals.
In Illinois in 1997, two professors from Northwestern University submitted a patent application for a joint invention. In the patent documents, J. Edward Colgate and Michael A. Peshkin described their invention as a new type of robot. It was designed to make direct physical collaboration with a person possible. Within just a few years, the name of their invention was widely known, and it is now a vital part of the history of robotics. The two professors called their brainchild a “collaborative robot”, or “cobot”. What’s more, in the same way as a human child learns to stand and walk with the help of their parents, it is only when you equip your cobot with suitable peripherals such as a base structure that it will show you what it is capable of. After all, you will only be able to use it to its full capacity when it can “stand on its own two feet”. This is where our modular profile technology comes into play, offering the ideal support. Our modular item Building Kit System offers you maximum flexibility when it comes to the peripherals for your robotic application.
Peripherals for robots from various manufacturers
In our interactive e-paper, you’ll find lots of sample solutions based on the item Building Kit System – complete with helpful videos and useful links.
Definition: robot peripherals as enablers
However, what exactly are robot peripherals? According to Dr. Stefan Hesse, who writes specialist books on the subject, this term covers pretty much everything a robot needs to become a turnkey robotic solution. In his book “Industrieroboterpraxis: Automatisierte Handhabung in der Fertigung” [English: Industrial Robot Practice: Automated handling in production], which is about industrial robot practice and automated handling in production, he writes: “Robot peripherals are all types of equipment that provide functions the robot is missing or execute functions more cost-effectively, and with which a robot works directly.” The term therefore covers camera systems and sensors, grippers and tools, programming and control interfaces, and power supply, for example. Robot peripherals also include base structures, which are essential for making integration in production possible in the first place. The same applies to linear units. In a practical project carried out at item in Solingen, students combined an item linear unit and a cobot. This means the robot now has a seventh axis. Conveyor belts for supplying materials and transporting them away are another element of robot peripherals.
Hesse continues: “Peripheral solutions should be flexible, and it ought to be possible to adapt them to new manufacturing conditions.” Although Hesse is talking about industrial robots in this case, you can also apply this sentence to robot peripherals for cobots. At the end of the day, the enormous flexibility of cobots is a key element in their cost-effectiveness – and this factor is even more important for SMEs. Thanks to simple programming and high levels of mobility, you can use one single cobot to automate a variety of processes. Popular examples include palletizing and machine loading and screw fixings and welding. When the peripherals facilitate rapid changeovers and can be adjusted with ease, they play a key role in the cost-effectiveness of the robot.
As versatile as robotics itself – peripherals with the item Building Kit System
You can find inspiring examples of flexible, easily adjustable peripherals in the sample solutions in the item Online Shop. Whether it’s a case of the partially enclosed cabin for using cobots, the mobile robot island with integrated cable management or the work bench with comprehensive equipment for collaboration with a robot, peripherals based on the item Building Kit System are modular, flexible and extendible. For example, why not turn a static base structure into a mobile one with ease, simply by attaching our lockable jacking castors? Alternatively, you could add a robot mounting plate and cobot to an existing item work bench, since the patterns of holes in our mounting plates have been optimized to accommodate cobots from popular manufacturers. By doing this, you will obtain a collaborative work bench – and all without compromising ergonomics. Whether you are automating new processes, integrating more robots or expanding the range of jobs they can do, robot peripherals based on our profile technology grow in line with your needs.
Example: work bench for human-robot collaboration
When it comes to customized robot peripherals in particular, the item Building Kit System really comes into its own. To put it more precisely, with more than 4500 compatible components at your disposal, you have all possible options available to you. In the images below, you can see a customized solution that was created at our European headquarters. The solution initially takes the form of a work bench for manual production. However, thanks to a docking device and mobile robot island, it can be converted into a work bench for human-robot collaboration within a matter of seconds. There are other advantages to using robotics in industry, too. You can use your cobot to ease the strain on your staff, for example, and to carry out small-series automated production.
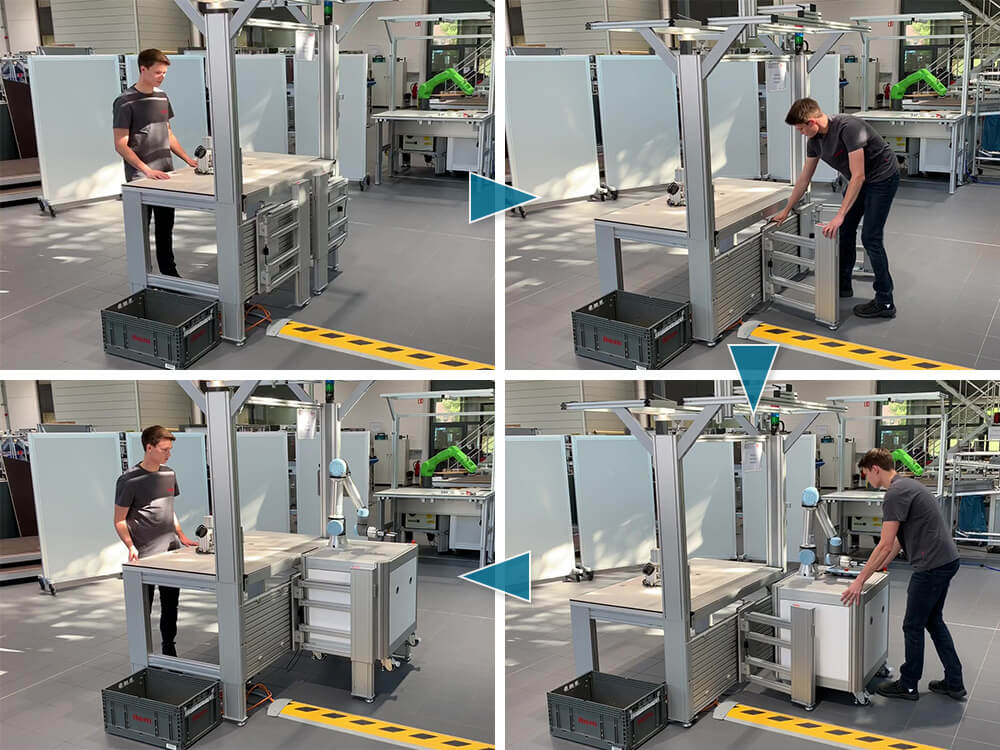
Robot cells ensure safety – even for welding tasks
As is evident from the patent awarded to J. Edward Colgate and Michael A. Peshkin – the “fathers of the cobot” – collaborative robots are designed for safe, direct collaboration with humans. This concept has its limits, however – for instance, if you want to use your cobot to perform welding tasks. In this case, robot peripherals such as a robot cell will provide the safety you need. This is demonstrated by the example of the “INNA” robot cell for automated welding, where a machine cabin based on our Line XMS is used. A robot cell of this type offers not only high levels of safety, but also sound insulation and dust protection. What’s more, the profiles in our Line XMS range, which has won multiple design awards, feature integrated cable conduits. You can open these up and close them again as you need to, so you can access all important cables from the outside, too.
INNA was developed by Inperfektion GmbH and Niederrhein Automation GmbH. When it came to choosing the welding robot, they deliberately decided to opt for a collaborative robot. After all, the ultimate aim is not only that INNA will help SMEs venture into the world of automated welding, but also that it will provide them with a simple introduction to automation. Wissam Nehme from INperfektion explains the benefits of cobots: “Since state-of-the-art lightweight robots are so easy to understand and operate, you don’t need any automation or programming experience to use them efficiently.” The automation specialists see huge potential in robot solutions, especially given the current skills shortage. More than two and a half decades after its “birth”, the cobot is therefore more relevant than ever before. As a tool for supporting humans, it is a true success story – and we are delighted to be able to play our part in this by helping companies integrate cobots.
Want all the latest updates on innovative robotics applications? Simply subscribe to the item blog by completing the box at the top right.