Lightweight robots are generally known for their exceptional flexibility. However, with the right support structure, they can truly reach their full potential.
Robots in industry can do a lot more than most people think and, thanks to the state-of-the-art lightweight designs available today, they are now more affordable and accessible than they were at the turn of the millennium – even for small and medium-sized companies. This is primarily due to their exceptional flexibility. With the wide range of end effectors available – such as suction cups and grippers for assembly and sorting, not to mention screwdrivers and welding heads – state-of-the-art industrial robots can be quickly retooled to suit a particular application.
On top of that, they are easy to program. Anyone who is at all tech-savvy can teach a lightweight robot the necessary motion sequences in just a few hours. What’s more, as the term “lightweight robot” suggests, they have a low dead weight of well below 40 kg in most cases. All these factors make it possible to have one of these robots perform autonomous welding tasks one day, and then equip it with a gripper and dock it to an industrial work bench for human-robot collaboration the next.
Robot tables, robotic racks, and more for robots in industry
To ensure robots are able to seamlessly switch between applications in this way and still perform reliably in general, they need a suitable support structure. This is where the flexibility of robots in industry and the versatility of item’s modular concept find common ground. The tried-and-tested aluminum profile technology makes it possible to engineer the perfect support structure for any application – and thanks to the wide range of standard components, this can usually even be done without any costly custom-made units. For example, the item portfolio includes ready-for-use mounting plates with bore grids that match common lightweight robots. This means smaller models of Universal Robots (UR3e, UR5e), for instance, can be attached to profiles and the groove plate using Mounting Plate 8 160 × 160. The 200 × 200 variant, on the other hand, is suitable for larger models such as the UR16e, the Fanuc CRX-10iA and various Omron models. Universal Mounting Plate 8 160 × 160 and 200 × 200 can be used for all other cobot and mechanical engineering solutions.
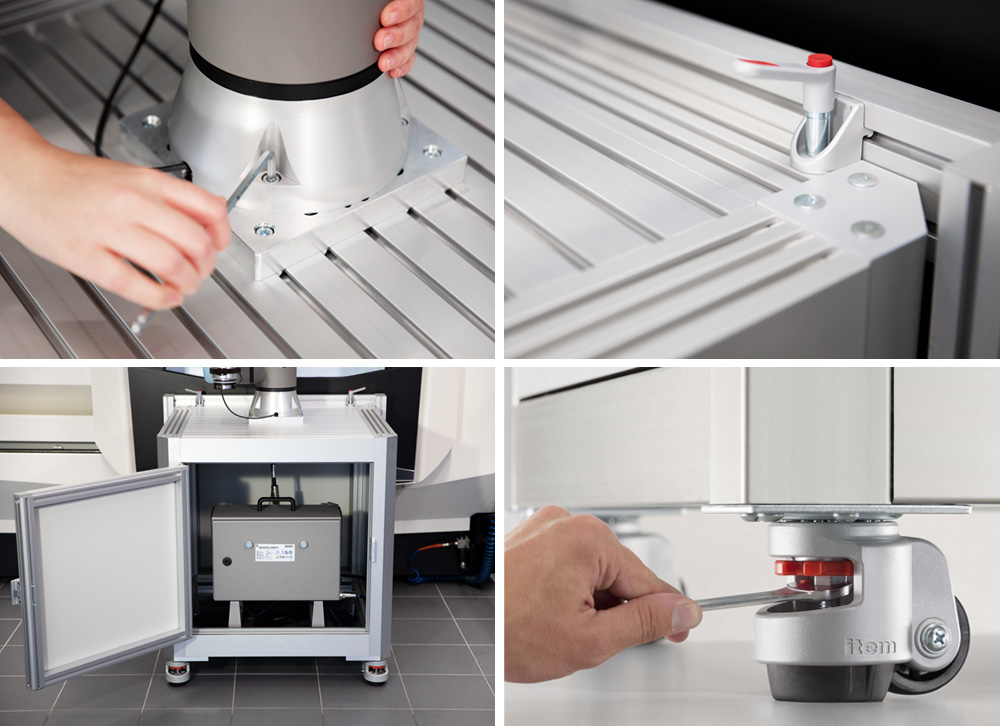
An example of a robot support structure with close-ups (clockwise): A cobot is mounted onto a groove plate with Mounting Plate 8. The mobile support structure is secured to a frame made of aluminum profiles using a clamp lever. Jacking Castors D62 can be locked for additional stability. The robot’s control box is safely stowed away in the built-in base cabinet.
Preconfigured robot support structures as a starting point and inspiration
This level of compatibility and modularity is a huge advantage when implementing robotics applications with item profile technology – and not just in a conventional industrial context, as robot manufacturer Franka Emika clearly demonstrated with the robot-based COVID testing station it developed. The light weight of the aluminum profiles is also a major plus, especially when it comes to building mobile robot cells that need to be moved from one place to another or retooled more frequently. In addition, base frames for robots in industry can be continuously optimized thanks to the exceptional adaptability and expandability of the constructions. If a construction that has already been implemented has to be ordered again – for another company location or another customer, for example – this is not a problem thanks to the permanent availability of all components worldwide.
Want all the latest updates on innovative robotics applications? Simply subscribe to the item blog by completing the box at the top right. For even more inspiration, discover the array of sample solutions on the item Solution Center, and learn from the best with robotics introductory courses on the item Academy.