At SAP’s Industry 4.0 Center, the full potential of digital production is a direct experience.
In the middle of the shop floor, an employee assembles components in one area supported by a robot. Nearby, a driverless transport vehicle brings parts to their destination. Data is received in real time for these and many other steps. What sounded like science fiction decades ago has long since become reality thanks to Industry 4.0.
The term “Industry 4.0” was coined in Germany in 2011 to describe the comprehensive digitalization of production, linking the virtual and real worlds. The example of a smart factory demonstrates the revolutionary nature of Industry 4.0: the data from this smart factory networked via the Internet of Things (IoT) goes beyond collection and analysis. Thanks to machine learning, it is also used to predict future events.
Powerful software is needed for these tasks. SAP SE is primarily known for its enterprise resource planning systems and financial software; however, it also has extensive expertise and solutions when it comes to Industry 4.0. Of course, the best way to see and understand such complex links between the offline and online worlds is with your own eyes. This is precisely why SAP invites you to the Industry 4.0 Center in Newtown Square, Pennsylvania: there, you can experience the potential of SAP Digital Supply Chain solutions for production and be inspired. SAP is working closely with numerous partner companies to equip the digital factory. item is pleased we were able to contribute to the factory equipment with modular solutions, as seen through the work tables created using our profile technology.
Industry 4.0 Center: Two digital supply chains in one place
The equipment in the digital factory includes various machines and systems, numerous item-based work tables, and driverless transport vehicles. An entire product life cycle is shown for two areas:
- Process industry (e.g. chemicals or food)
- Discrete manufacturing (including mechanical engineering and the automotive industry)
Germany and Japan each have an SAP Center for Industry 4.0 with an identical concept where visitors see an absolutely realistic process. “We show a real-life end-to-end scenario,” explains Rakesh Gandhi, Vice President of Digital Supply Chain and Industry 4.0 Centers at SAP. Gandhi continues “you can see our portfolio for the digital supply chain live in action – for processes involving design, planning, manufacturing, logistics, operations on the store floor, and maintenance.”
SAP covers all areas of the digital supply chain with holistic solutions. For example, the application example for discrete manufacturing follows the path of a double-seat valve, frequently used in the beverage industry. In the Industry 4.0 Center, you can experience all the steps of the double-seat valve in the digital supply chain firsthand. This illustrates one of SAP’s central ideas: “Design to Operate.”
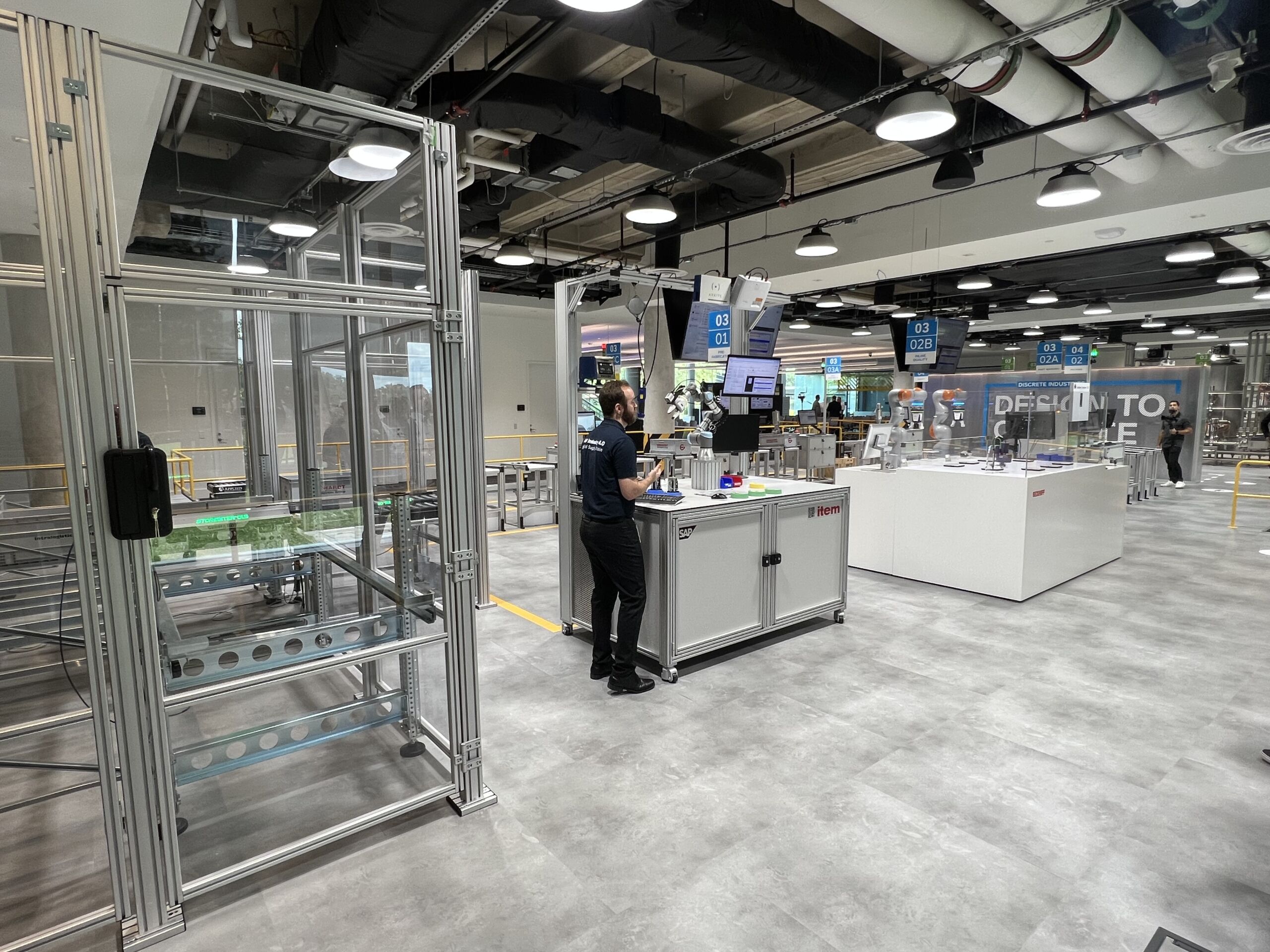
From the warehouse enclosure (left) to the work table (center) and the transfer station for driverless transport vehicles (in the background): The Industry 4.0 Center demonstrates the versatility of the item modular principle.
Meeting current challenges perfectly with SAP and Industry 4.0
Parts, products, and processes are digitally linked, with data being generated in real time. For SAP, two concepts play a decisive role here: vertical integration and interoperability.
Vertical integration means that the software has a direct connection to the shop floor, where data flows directly in to enable precise planning, control, monitoring, and optimization.
Interoperability refers to the ability of different systems to communicate with each other and exchange data. In the Industry 4.0 Center, SAP demonstrates why its own solutions are perfectly suited for this. Due to current developments, Industry 4.0 is more relevant in North America than ever before.
“A lot has happened in the last three years,” explained Rakesh Gandhi. “More and more manufacturing is moving back into the US. This demands highly developed automation as well. Some customers are highly automated, others only in some aspects, others are at the beginning. We help customers to define their journey.”
A manual workstation shows that manual assembly in a smart factory is not a thing of the past: the table based on the item Building Kit System was designed for human-robot collaboration. Here, employees assemble electronic components using a precision screwdriver. Thanks to a special robot mounting plate, a cobot from Universal Robots is perfectly integrated into the table. Our robot mounts are available for all common cobot models. In addition, there are universal mounting plates into which you can insert individual drilling patterns and machining operations. There is a camera on the cobot, which feeds the necessary parts to the employee. The precision screwdriver, robot, and camera are digitally networked on the robot table, creating a data model to use this information, enabling a virtual inspection of the assembly in SAP Digital Manufacturing. This Manufacturing Execution System (MES) and the ERP system SAP S/4HANA Cloud are the key SAP solutions for Industry 4.0.
Maximum design freedom thanks to item profile technology
“Whether ergonomics or software solutions: in a factory, you have to look at everything. And item provides knowledge for workstations plus many more things. This helps customers in a very dynamic way to build up their factory at a faster pace,” said Gandhi. item profile technology is not only found in the aforementioned robot table, but in fact, all table constructions in the Industry 4.0 Center were designed with item profiles. Ralf Lehmann, Solution management for Digital Manufacturing and Industry 4.0, is responsible for the identically constructed Center in Germany. Lehmann explained, “work furniture from item is used wherever employees are working. When it comes to storage areas for tools, the IT infrastructure or monitors with assembly instructions, the basis is always an item work surface.”
In addition, the warehouse enclosure is made of aluminum profiles, acting as a transfer station for driverless transport vehicles. In addition, a rack for lean material provision is also used, consisting entirely of components from our lean production modular system. The flexibility of our modular principle comes into its own in all designs. All requirements in terms of spatial dimensions, working height, and storage space could be met exactly. The realistic design and numerous well-known manufacturers ensure a direct recognition value: “the ecosystem of our partners shows what is possible with Industry 4.0. That is the decisive factor in this collaboration. If you have a cobot, it doesn’t work without an ergonomic table. And the solutions of item play a key role in this live environment,” emphasizes Rakesh Gandhi.
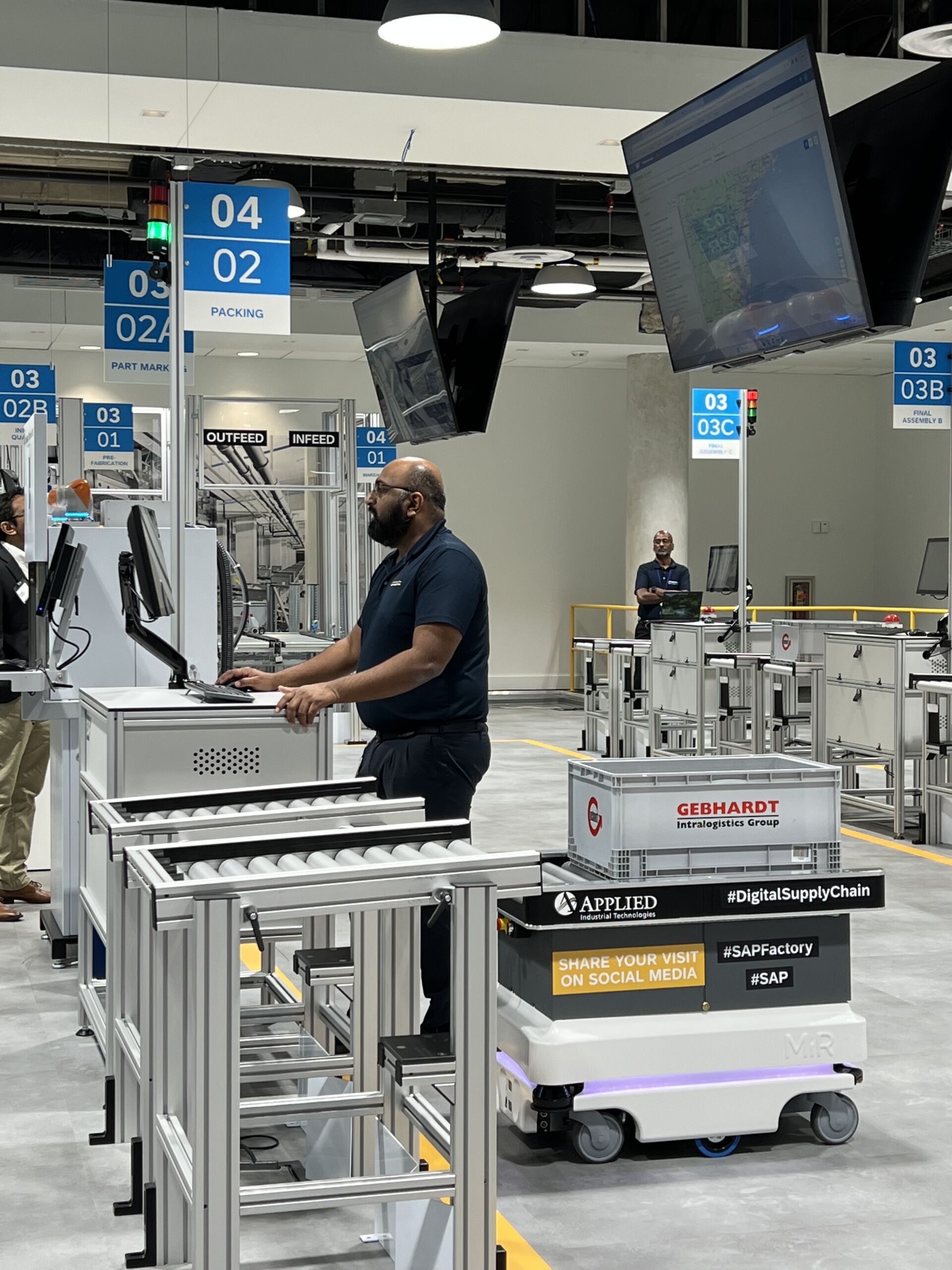
SAP also relies on item modular components for these transfer stations for driverless transport vehicles.
Would you like to immerse yourself in the fascinating world of Industry 4.0? Whether you already use SAP solutions or are simply interested in digital production, you are very welcome at the Industry 4.0 Center.