Despite the innovations associated with digitalization and Industry 4.0, manual work is still indispensable in industry.
Most manual operations are highly repetitive. According to the 2018 health report of Techniker Krankenkasse (a German statutory health insurance provider), musculoskeletal ailments are in general the primary cause of employee absenteeism. Especially in the case of industrial assembly work benches, it is therefore essential for employers to comply with the principles of ergonomic workplace design. Doing so offers nothing but benefits for everyone involved, as item ergonomics expert Marius Geibel explains: “Ergonomics is often seen as an unnecessary and costly way of trying to turn the workplace into some kind of health spa. In a holistic approach, however, improving productivity is an integral aspect of ergonomics. In practical terms, ergonomics and efficiency go hand in hand. Personnel who are not under unnecessary strain are more motivated and perform better. Ergonomics helps companies retain their workforce for the long term.” This post aims to explore the various interlinking factors that create an ergonomic assembly work bench.
Height-adjustable assembly bench and industrial chair
Working for several hours in the same position soon takes its toll, causing strain that can develop into chronic pain in the long term. Wherever processes allow, employees should therefore be able to switch between sitting and standing as they do their work. One quick way of achieving this and relieving strain is to use a height-adjustable assembly bench, ideally one that can be raised and lowered electrically. Humans are not meant to sit for long periods. Doing so has only been part of our everyday (working) lives for around 250 years, so it’s advisable to switch to working standing up after sitting for a while.
Ultimately, of course, sitting at an assembly work bench is unavoidable. When selecting industrial chairs, a number of factors therefore need to be considered. Just like assembly benches, chairs should also be steplessly adjustable in height, which is why an assembly work bench system like the one offered by item covers both these requirements. Chairs’ customized adjustment options should encourage dynamic sitting, whereby employees avoid uneven strain and overtaxing of individual muscle groups by changing their position and posture as often as possible. Other key requirements for industrial chairs include robust materials and stability when shifting weight.
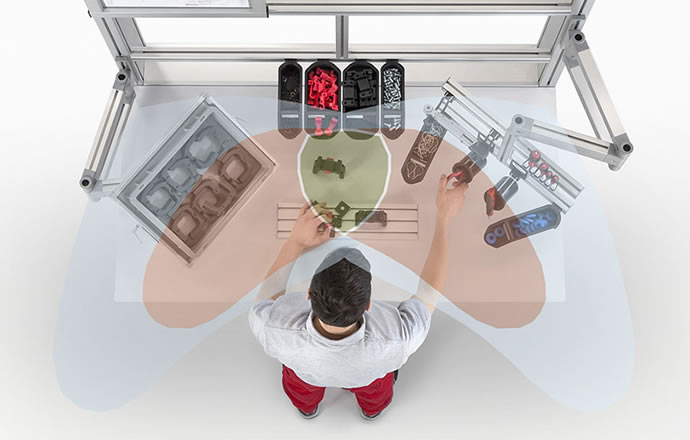
A different handling area applies to each and every employee.
Importance of the handling area for assembly work benches
The handling area has a big part to play in the design of an assembly work bench. There are several ways in which it can vary. A distinction can be made between the outer handling area (accessible with the arm outstretched) and the inner handling area (can be reached with the arm bent). The area can also be divided into three different zones. The two-handed zone is located directly in front of the operator – that is to say where the process is actually carried out. Materials and tools that are required on a regular basis should therefore be placed in this zone to make them easy for staff to access without having to turn their body to do so. By contrast, working materials are within reach using a single hand in the one-handed zone. Last but not least, the extended one-handed zone covers the outermost part of the handling area.
The various zones of the handling area differ for each person, though, so each and every employee must be able to adapt material provisioning and picking at the assembly work bench to their particular needs to avoid poor posture. This can be specifically prevented, for instance, by using pivot arms to place tools in the one-handed zone. Components ranging from parts containers to hooks and holders for tool provision and stowage are easy to attach to these arms.
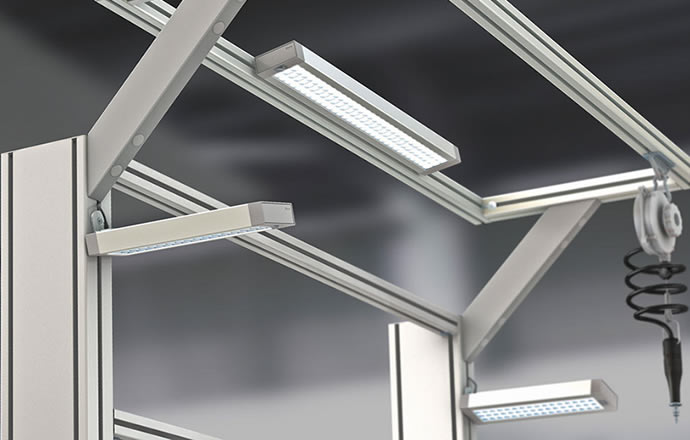
The importance of having the right lighting should not be underestimated, as this also relieves strain.
Ergonomic lighting at the assembly work bench
Lighting is a factor that is often overlooked in assembly work bench ergonomics, but here, too, ignoring ergonomic principles can prove detrimental. Even the light color of an LED light fitting affects staff’s health and thus their performance. The following basic rules apply to light color:
Cold white light has a stimulating effect on people (3330 to 5300 Kelvin)
Warm white light creates a relaxing, calming atmosphere (2700 to 3300 Kelvin)
With that in mind, it’s important to ensure a good balance when lighting an assembly work bench. A light color of around 4000 Kelvin is recommended. This lies between the warm white illumination of a light bulb (2500 to 2700 Kelvin) and normal daylight (5800 to 6500 Kelvin).
The phenomenon of individual spotlights creating superimposed hard shadows – known as multiple shadows – can also cause eye strain, quickly leading to clear signs of fatigue and lapses in concentration. The homogeneous illumination of an LED industrial light, on the other hand, produces only soft shadows, which place the eyes under far less strain. This is even the case with flicker-free light from high-frequency LED industrial lights. Anything else is counter-productive at an assembly work bench, because even low-frequency flickering that is not readily perceivable causes strain.
Do you want to stay up to date with assembly work bench developments?
Then we have something that’s right up your street!
Simply subscribe to the item blog by completing the box at the top right!
.