Reflections on a growing trend in the Continuous Improvement world
As manufacturers strive to find strategies to increase efficiency, lower costs, and improve safety, more and more companies are turning to low-cost automation to reach their goals. There are many technological resources to implement automation and they can be very effective; however, these automated systems can also be extremely expensive and longer lead times to bring them into service are common.
A continuous improvement tool that has been particularly useful for industrial manufacturers and material handlers is karakuri solutions. Karakuri is a low-cost automation application that uses gravity, inertia and the weight of the article being moved to automate a process. This can be easily and ergonomically actuated by an employee or using a simple drive or other timed actuator to set the process in motion. The result is an automated process that improves efficiency for a fraction of the price of fully automated systems.
An added benefit of using karakuri to make a process more lean is that it can be built, adjusted and adapted to changes to process in-house. In the case of item’s Lean Production System (LPS) D30 line, a few basic hand tools and a little ingenuity can allow a facility’s in-house team to quickly adapt different iterations to improve a line in real time. No need to shut down a line for a programmer to come in and reset all the automation systems to the new configuration!
By developing the LPS line for karakuri applications, item is putting the control back in manufacturers’ hands. Through a combined approach of design and assembly, education and training and a wide range of parts and accessories, item’s LPS line enables companies to perform continuous improvement actions as they need to. While larger companies might have a Kaizen team devoted to these activities, having such a team is not necessary. item seeks to enable the end user to actively participate in and then own their own improvements, no matter how big or small the operation may be.
Karakuri: A Growth Equation
In 2019 alone, item saw a substantial increase in interest in karakuri applications with many more solutions being built and shipped. While an almost 80% year-over-year increase in karakuri orders is fantastic news, item is committed to training and supporting companies that want to develop their own in-house low-cost automation assembly process.
Tim Coy, the Team Lean lead at the item America headquarters in Hagerstown, Maryland, is working hard to develop training programs for customers interested in bringing karakuri into their continuous improvement program. Regarding the training, Coy stated, “the main vision I have for the karakuri training is that I want it to be a course that people will want to take. I want people to leave each day of the training and be excited for what they will learn the next day just as I was. Karakuri is fun and that’s my plan for the training – I want it to enjoyable with still learning everything I can teach them in the time we have together.”
A basic outline of the course will look something like this:
- Day One: Introduction to the LPS building system profiles and connectors.
Participants will then begin building a flow rack using LPS. - Day Two: Introduction to the basic principles of karakuri.
Participants will add a simple karakuri function to the flow rack built on Day One. - Day Three: Introduction to advanced karakuri.
The simple karakuri from the previous day will be upgraded to a fully functioning karakuri flow rack with moving parts.
Coy finished, “once all is said and done they will be ready to return to their company and build on their own with our products.”
When asked about the growth of interest in karakuri, Coy went on to say, “I foresee another huge jump in karakuri sales and customer base in 2020 for sure. The karakuri team has been growing along with our knowledge of this way of building and I hope to continue this growth to help item countrywide to get where we are at the headquarters.”
Industry Trends
Manufacturing and material handling professionals are taking notice. In Michigan alone, item North America Regional Sales Manager, Brandon Cross shared a couple of success stories where major automotive companies reaped benefits from item karakuri solutions. In one case, a large auto parts packing and distribution plant manager used a karakuri application to provide an ergonomic solution for a highly repetitive process that involved constant bending to pick up rejected packages.
In a more striking way, Cross shared another instance where a truck assembly plant used karakuri to great advantage. This plant had a process that involved unused liquid sealant being purged into a small tote. When full, the line was required to completely halt production for the bin to be physically emptied and replaced by an hourly employee. In addition to the risk of injury, this routine stoppage led to lost production time. By implementing a simple karakuri solution, this plant was able to eliminate this problematic stoppage. In all, the manufacturer estimates $250,000 in annual labor costs savings – all thanks to a $3,000 karakuri application!
Ben Hull, a Regional Sales Manager for item in Maryland and West Virginia, has received similar feedback from manufacturers in his region. Among them, an international health and beauty corporation has started using karakuri solutions to streamline production and material handling processes in its West Virginia plant. Hull also mentioned that a heavy truck components manufacturer he serves in Maryland “loves” that the LPS D30 comes in a heavy-duty version. The D30 Heavy has the same outside diameter as the regular D30 pipe but with thicker walls. The same connectors work for both lines!
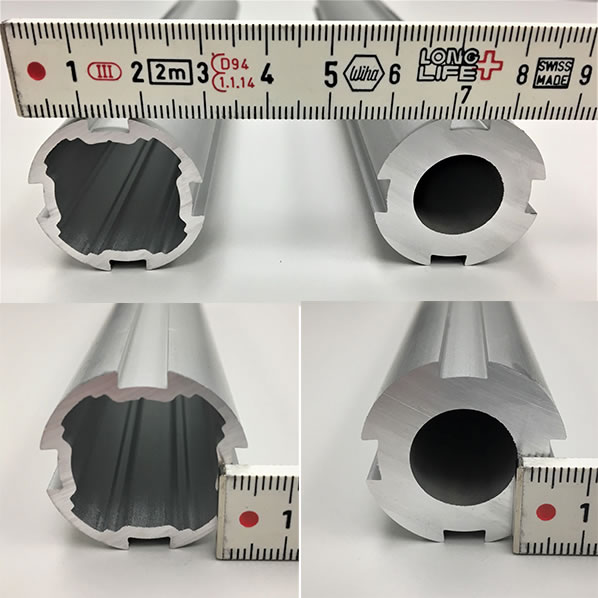
Line d30 comparison
These examples focus largely on manufacturing production and material handling solution, but the flexibility and adaptability of the item LPS Building System lends itself to many other applications. What doesn’t change is the user’s ability to take an idea and make it happen with a few simple tools and a clear concept.
Are you looking to economize a process that needs better lean efficiency?
Be at the forefront of a lean solutions trend with item. You can learn how karakuri and low-cost automation might benefit your operation and then how you can realize your own ideas by partnering with item!
.